BiG X 680 ∙ 780 ∙ 880 · 1180, the XXL forage harvesters from KRONE for outputs of 687hp to 1156hp. They not only impress by their high efficiency and chop quality but also by high operator comfort and easy handling.
- High-power and fuel efficient engines from 687hp to 1156hp
- 6 intake rollers for boosted reliability and a top quality chop
- MaxFlow chopping drums with 20, 28, 36 blades; Biogas drums with 40 and 48 blades
- Roller and disc conditioners for all applications
- KRONE VariLOC for flexible choice of long and short chops
- KRONE VariQuick for fast changeovers to conditioning or grass cutting
- Convenient hoop coupler for easy attachment to the base machine
- Enormous agility from independent wheel suspension
- Height-adjustable comfort cab for optimum visibility
Product features
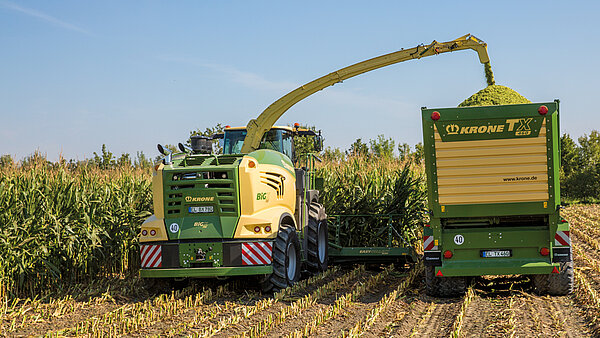
- 6 intake rollers for maximum reliability and best chop quality
- MaxFlow chopping drums with 20, 28, 36 blades, biogas chopping drum with 40 and 48 blades
- KRONE VariLOC: flexible use in long and short cut
- OptiMaxx roller conditioners with up to 305 mm diameter, 710 mm width and slanted teeth for intensive kernel conditioning
- KRONE VariQuick: quick changeover for working with and without corn conditioner
- KRONE VariStream: Continuous crop flow ensured by spring-loaded floors for chopping drum and discharge accelerator
- Powerful and low-emission engines from 687 to 1,156 HP
- Great manoeuvrability from independent wheel suspension: For extreme manoeuvrability
- Height-adjustable comfort cab: For optimum visibility
BiG X 680 – 1180, these are the extra powerful forage harvesters from KRONE with an output of 687 to 1,156 HP. They impress not only with their high output and chop quality, but also with their comfort and handling.
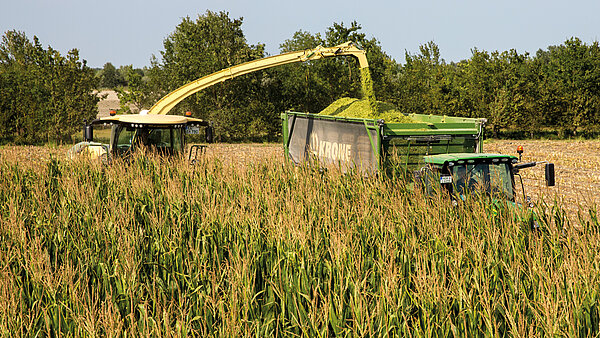
- KRONE chopping technology for optimum maize forage quality
- OptiMaize S, M, L, XL for variable chopping lengths from 4 mm to 30 mm
- KRONE MaxFlow and Biogas drums with different blade specifications combine for producing the
chops length you need - KRONE OptiMaxx roller conditioners ensure optimum fracturing and kernel treatment
- KRONE VariLOC for flexible long and short chops without conversing the machine
OptiMaize brings full flexibility to all KRONE BiG X harvesters, allowing them to produce any type of chop length livestock farmers and Biogas producers call for. MaxFlow and Biogas drums are available with various numbers of blades and combine with matching KRONE conditioners to deliver perfect 4-30 mm (0.2"-1.2") chops and the most intensive treatment. The BiG X offers this wide range of chops without operators having to swap or refit the chopping drum – simply by reducing the cutting frequency with the help of VariLOC.
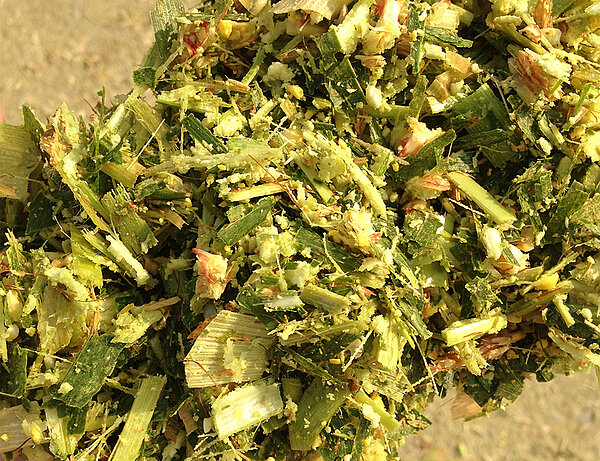
The maize in dairy feed rations made up of more than 80% by maize and that do not contain sufficient quantities of grass and feed straw should be chopped to 20 mm to 30 mm lengths to avoid lack of structure in the feed. The ideal drum for long chops is the MaxFlow chopping drum with 20 blades which is complemented by the KRONE OptiMaxx roller conditioner with 105/123 teeth and 30 %, 40% or 50% speed differentials.
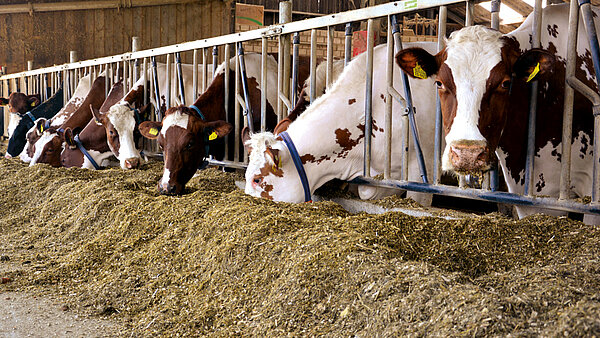
Cutting lengths of 11 to 19 mm are ideal for dairy cattle with a maize content of around 60 % in the forage ration. Rumens require silage maize that is reach in fibres. The OptiMaize L chopping quality is achieved by the KRONE MaxFlow chopping drums with 28 or 20 blades. KRONE OptiMaxx roller conditioners with 105/123 teeth, whose speed difference can be increased from 30 % to 40 % or 50 %, are recommended as conditioning units.
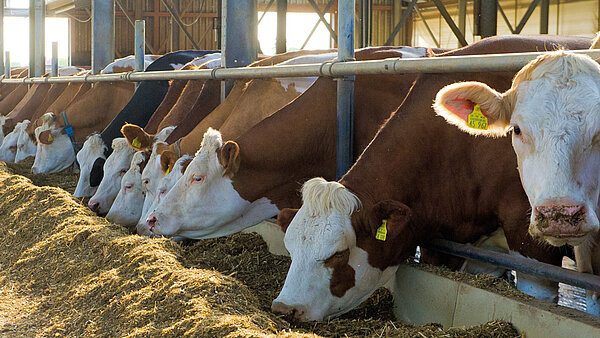
Grass based rations for beef bulls and dairy cows which consist of up to 40 % of maize should be made up of 8 mm to 10 mm (0.3" to 0.4") chop lengths. This length of cut and an appropriate conditioning intensity avoids lack of fibre in the ration. OptiMaize M chopping quality is achieved by the MaxFlow drums with 36 and 28 blades. The ideal conditioner is the KRONE corn conditioner with 123/144 teeth whose speed differential can be increased from 30 % to 40 % or 50 %.
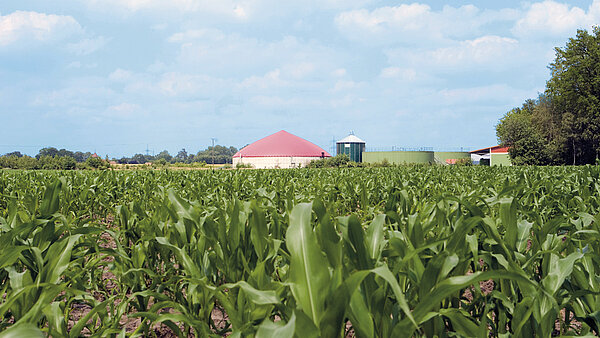
Maize that is harvested to fuel biogas plants is chopped to very short lengths. Depending on moisture levels, chops of 4 mm to 7 mm lengths have been found ideal for this application, because shorter chops make the energy readily available to the methane producing bacteria in the fermenter thereby increasing gas yields. The KRONE forage harvesters use a Biogas drum with 40 or 48 blades to harvest biogas maize. Alternatively, OptiMaize S results can also be achieved with the 36 blade MaxFlow drum. For good fermentation, the leaves and stalks are subsequently fractured and the kernels destroyed by a KRONE corn conditioner with 123/144 teeth and rotors rotating at a 30 % speed difference.

The OptiMaize concept was developed by KRONE and aims at producing forage of a superior quality. Livestock farmers ask for different chop lengths that meet different aims in the silage maize ration. The smaller the amount of fibres in the ration, the longer should the maize chops be to suit the needs of rumens. By comparison, chop lengths should be short when the maize is used to fuel Biogas plants whereas the feed rations for beef bulls and dairy cows require much longer chop lengths to add structure to the ration. KRONE OptiMaize combines various chopping drums (see table) and conditioners that enable BiG X forage harvesters to produce short and long chops of maize allowing machine owners to respond to individual customer needs. Where, for example, finely chopped energy maize needs to be harvested in the morning and coarsely chopped forage maize for the cattle at midday, the KRONE VariLOC is the ideal solution. This manual gearbox, which is integrated into the pulley of the chopping drum, can reduce the drum speed from 1,250 to 800 rpm within a few minutes. This reduces the cutting frequency and increases the range of available chop lengths by up to 50%. In this way, it is possible to choose between short and long cut at short notice without the additional expense of converting the drum. This in combination with the KRONE OptiMaxx roller conditioners makes BiG X a truly all-round machine. The chop length can be grouped into four different ranges: OptiMaize S, M, L, XL. Each concept describes a different technical solution that leads to customised lengths that suit all applications.
The OptiMaize concept was developed by KRONE and aims at producing forage of a superior quality. Livestock farmers ask for different chop lengths that meet different aims in the silage maize ration. The smaller the amount of fibres in the ration, the longer should the maize chops be to suit the needs of rumens.
By comparison, chop lengths should be short when the maize is used to fuel Biogas plants whereas the feed rations for beef bulls and dairy cows require much longer chop lengths to add structure to the ration. KRONE OptiMaize combines various chopping drums (see table) and conditioners that enable BiG X forage harvesters to produce short and long chops of maize allowing machine owners to respond to individual customer needs. If you have to produce short biogas maize chops in the morning but coarse maize chops for animal feed in the afternoon, you will find KRONE VariLOC the ideal solution for you.
This manual gearbox, which is integrated into the pulley of the chopping drum, can reduce the drum speed from 1,250 to 800 rpm within a few minutes. This reduces the cutting frequency and increases the range of available chop lengths by up to 50 %. In this way, it is possible to choose between short and long cut at short notice without the additional expense of converting the drum. This in combination with the KRONE OptiMaxx roller conditioners makes BiG X a truly all-round machine.
The chop length can be grouped into four different ranges: OptiMaize S, M, L, XL. Each concept describes a different technical solution that leads to customised lengths that suit all applications.
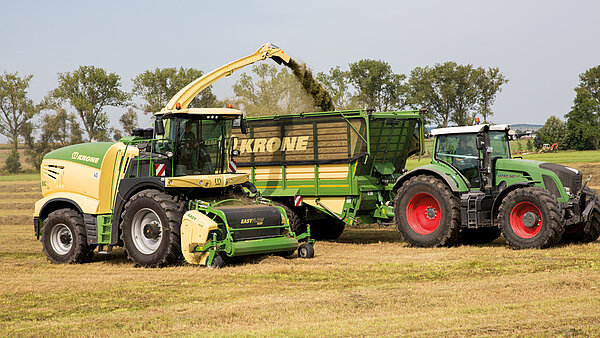
- Six intake rollers ensure a top-notch quality of chops
- High throughput with universal and biogas drums
- OptiMaxx roller conditioners for intensive kernel processing
- Flexible chop lengths through VariLOC and the use of only half the number of blades
- Continuous crop flow from VariStream
- Variable crop throw is an option using StreamControl
- Quick changeovers between corn and grass thanks to VariQuick
Its innovative technology makes the BiG X a superior chopper with respect to performance and quality. Chopping lenghts can be set to individual requirements by adjusting the speeds of the intake rollers and using different numbers of blades on the chopping drum. Highest through puts are implemented by the spring-loaded floor underneath the drum and a spring-loaded accelerator backplate which guarantee a continuous crop flow.
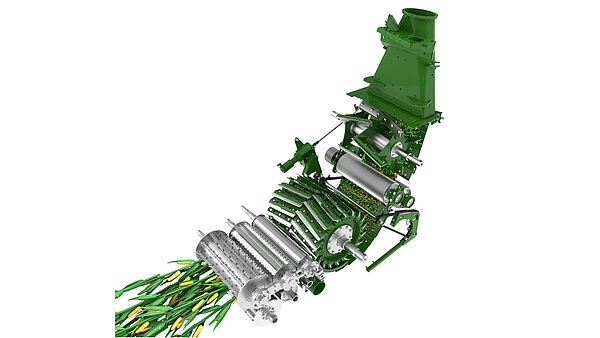
Intake system
Helps achieve the desired chop length
- 6 hydraulic intake rollers
- The speed is set steplessly from the cab
Chopping drum
The guarantee for top quality chops
- MaxFlow chopping drums with 20, 28 or 36 blades
- Biogas chopping drums with 40 and 48 blades
StreamControl
- Powerful discharge accelerator
- Adjustable discharge distance
- Precise loading of downstream transport units
- Reduced power requirement for parallel loading
- Working without losses
The OptiMaxx roller conditioners
- Rollers with 250 or 305 mm diameter and 710 mm width for maximum performance
- Slanted teeth give a unique shearing effect for perfect cracking
- Up to 50% speed difference for optimum fracturing results
VariQuick
- Minimum changeover time between grass channel/corn conditioner
- Quick changeover for working with corn conditioner or grass channel
- Convenient removal of the corn conditioner using mechanical pivoting unit
VariStream
- Maximum throughput
- Spring-loaded chopping drum floor
- Spring-loaded rear wall of discharge accelerator
- Continuous crop flow even with uneven crop feed
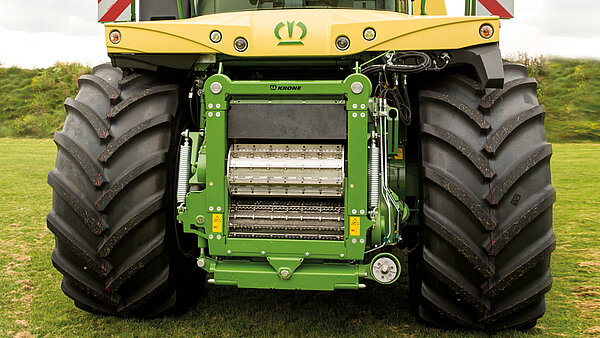
- Hydraulic drive: The chop length is steplessly adjustable from the cab
- Automatic setting of the chop length via AutoScan or NIR sensor
- 6 pre-compression rollers for top-quality chops
- Perfect protection from foreign objects: Long path from the metal detector to the chopping drum and metal detection across the entire width of the channel
On a BiG X, it is also the intake system that has an influence on the quality of chop. The six intake rollers continuously press the chopped material with high pressure so that it can be chopped more easily and precisely. The hydraulic drive of the infeed elements allows manual or automatic adjustment of the cutting length.
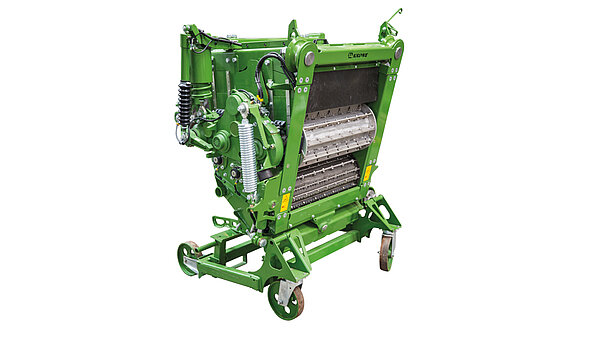
For inspection and maintenance purposes on the chopping unit, the intake can simply be set down on a transport frame.
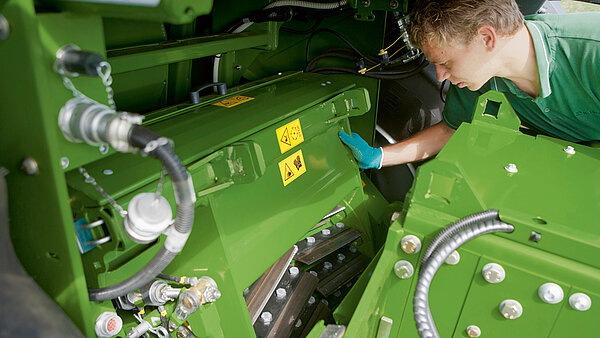
Operators can fold the intake system forward to gain access to the chopping drum and the counterblade.
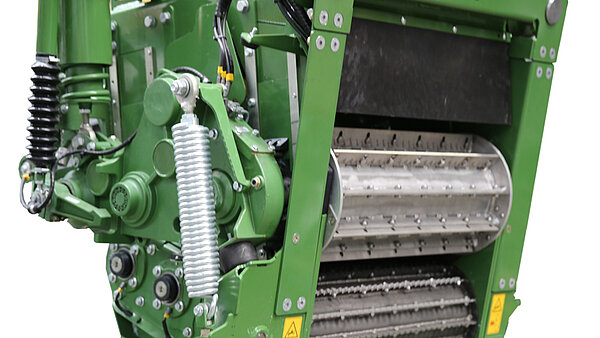
A system of pushing and pulling springs on the intake rollers combines to give maximum and consistent precompression in this area.
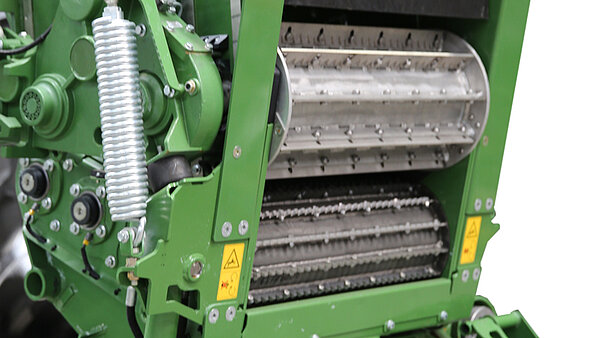
The leading bottom rollers are studded with sensors across the full width which detect any metal that is about to enter the machine. The large throat volume makes for highest throughputs. The robust drives withstand the highest strains.
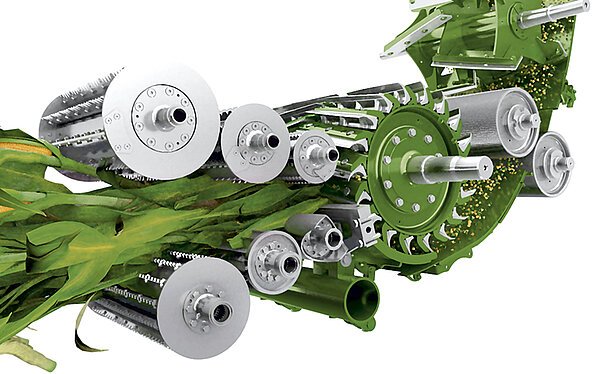
Six pre-compression rollers and the 820 mm gap between the leading roller with metal detector and the counterblade not only enhance pre-compression but also protect the blades better against metal objects, even at high-speed intake. The hydraulic drive in combination with AutoScan adjust the chop length automatically to the maturity of the crop.
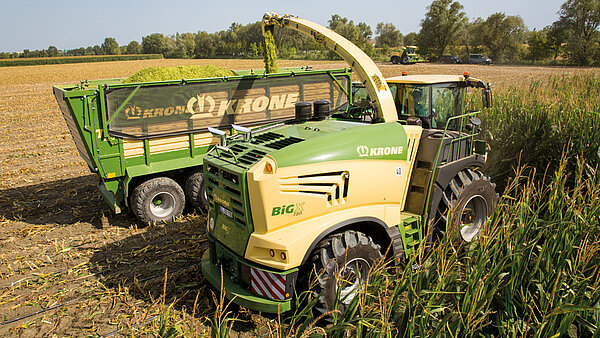
- KRONE chopping drums with 20, 28, 36, 40 or 48 blades
- High flywheel mass Closed drums with a diameter of 660 mm
- Top chop quality Drums with a width of 800 mm matched to BiG X 680 – 1180
- Low fuel consumption High flywheel mass, pulling cut
Matching the drum dimensions to the forager model
and choosing the optimum number of blades not only
boosts machine power but also makes the forager
more flexible to suit more applications. The wide range
of OptiMaize drums that are available for BiG X deliver
top-quality chops in versatile applications anywhere in
the world.
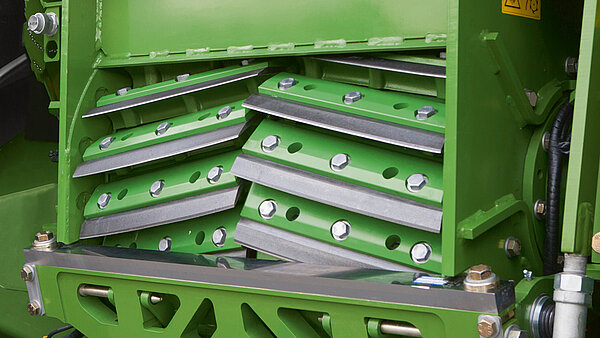
Protected drum body The carrier bars of the blades have another function besides: they protect the closed drum from wear.
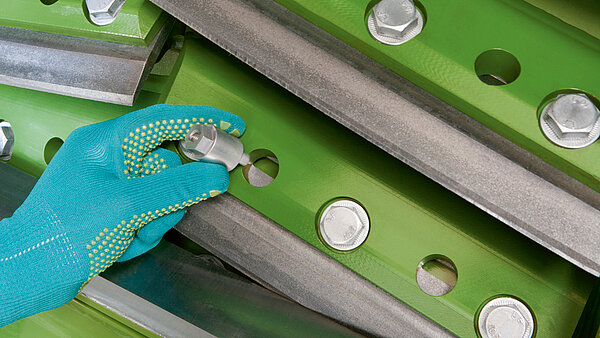
To ensure a good quality cut, the blade and the counterblade must be set to the correct gap. The blades are quick and easy to align using the eccentric plate.
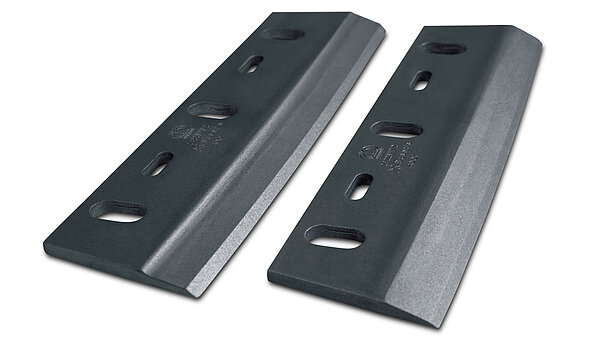
BiG X can be fitted with grass or maize blades. Slots on the blades allow for precision adjustment relative to the counterblade and protect the blades against breakage when they hit foreign objects..
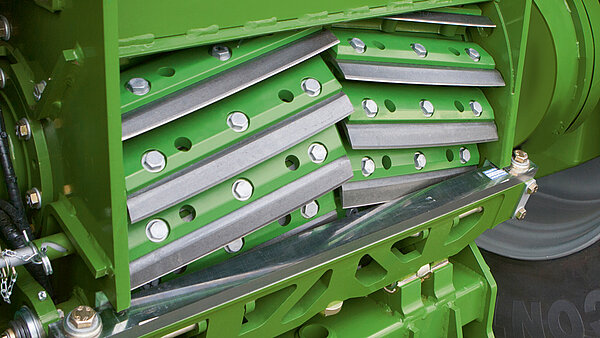
The blades on the KRONE chopping drums are arranged chevron-style and at an angle of 11° relative to the counterblade. This arrangement makes for a continuous crop flow, extremely quiet running and maximum efficiency.
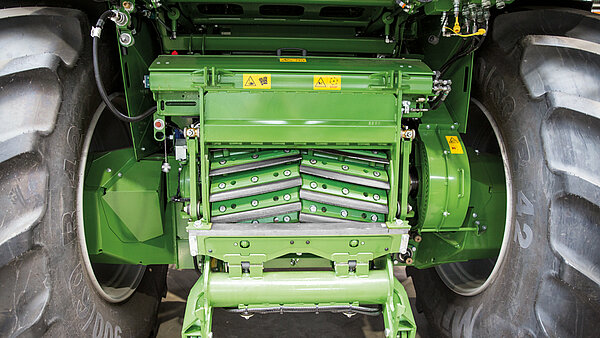
It's not just the number of blades that accounts for a good quality chop.The thickness of the mat that passes through them and therefore the width of the chopping drums are just as important. The 800 mm KRONE MaxFlow and KRONE Biogas drums on the BiG X 680, 780, 880 and 1180 guarantee just that.
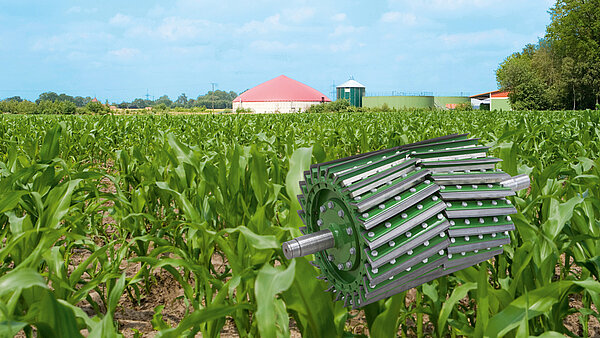
- 40- and 48-blade Biogas drums for OptiMaize S results
- High cutting frequency, fewer overlengths
- Very economical: high throughput at low consumption
- Short chops for high gas yields
The KRONE Biogas drum with 40 or 48 blades chop the material very intensively. OptiMaize S achieves very short chops which enable high throughputs both on the machine and in the fermenter, making BiG X a major factor in biogas plant productivity.
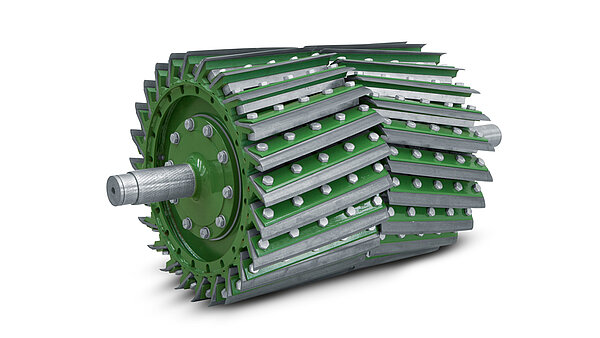
Delivering a 20% higher cutting frequency than the 40-blade drum and a theoretical LOC ranging from just 2 to 12 mm, this Super Biogas drum with 8 blades produces an even shorter chop, Boosting gas yields and throughput at the biogas plant even further and reducing fuel consumption per tonne of crop with the same LOC.

Chopping the crop to short lengths, the KRONE Biogas drum with 40 blades increases throughput by nearly 25% over what is achieved by a standard 28-blade drum.At the same time, fuel consumption drops by approx. 16% per tonne of chopped material.
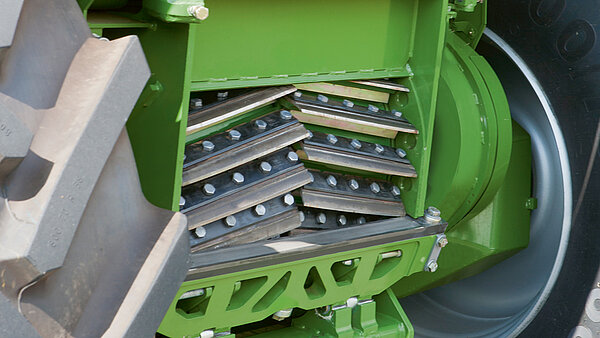
40 blades can achieve an impressively high cutting frequency. So the Biogas drum cuts harvesting time and increases throughput – even when producing short LOCs.
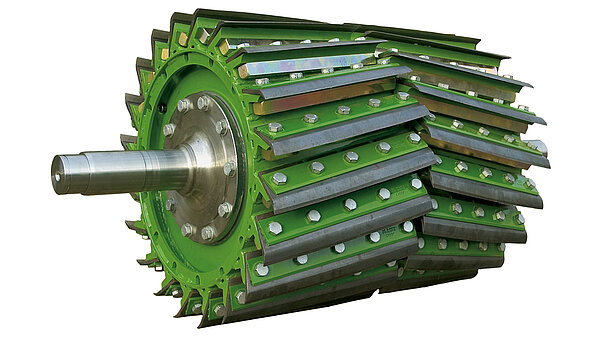
With its higher throughputs and lower fuel consumption per tonne of chopped maize, the 40-blade Biogas cylinder pays for itself in no time. The extremely short chops of 2.5 mm to 15 mm ferment at a higher rate and increase the gas yield, allowing farmers to produce more biogas from a smaller field.
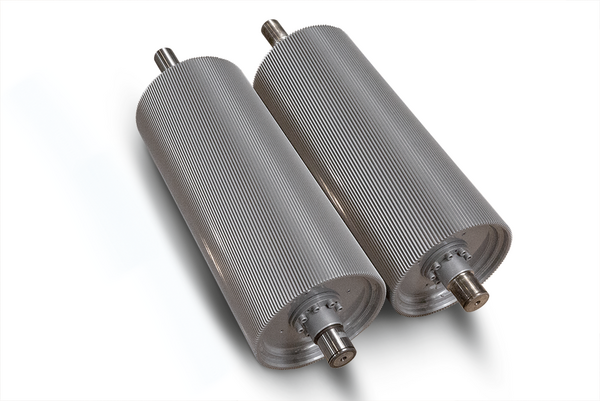
- OptiMaxx roller conditioners with 250 or 305 mm diameters
- Slanted teeth for perfect conditioning to combine with OptiMaize S-XL drums
- The gap between the rollers is conveniently adjusted from the cab
- A strong spring assembly provides a consistent and high pressure
- Maximum fracturing from an up to 50% speed difference (option)
- BusaCLAD-Special coating technology for maximum service life
Every single kernel must be cracked to achieve an optimal digestibility. These user demands are perfectly met by the new OptiMaxx 250/305 roller conditioners with their slanted teeth, a new KRONE development.
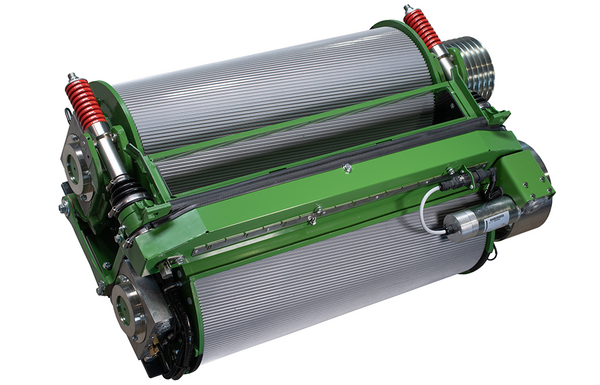
OptiMaxx 305 was developed to bring more chopping power to the high-capacity BiG X 680/780/880/1180 models.Offering a 55 mm larger diameter than the OptiMaxx 250, this roller conditioner is the perfect match for the gargantuan appetite of these top-end foragers.
- 305 mm diameter rollers with oblong teeth give a special shear effect
- A 11 % larger friction surface area and 20 % higher peripheral speed (than OptiMaxx 250) ensure an exemplary crop intake, intensive conditioning and optimum cracking amid high throughputs and long chop lengths.
- Stronger and more powerful springs apply a uniform, constant and high pressure on the crops
- A redesigned casing with beefier mountings ensures durability and longevity
- Temperature sensors on the roller bearings transmit the data to the operator terminal and ensure maximum safety
- Exemplarily easy to service and maintain thanks to large openings. Bearings, rollers and pulleys are replaced quickly and cleaning is as easy.
- The two rollers in the assembly have different numbers of teeth:
– 125/150 for medium and long chopping lengths
– 150/175 for short and medium chopping lengths - A standard 30% or optional 40% speed difference for intensive fracturing and optimum cracking results
- BusaCLAD-Special coating technology as an option for maximum service life
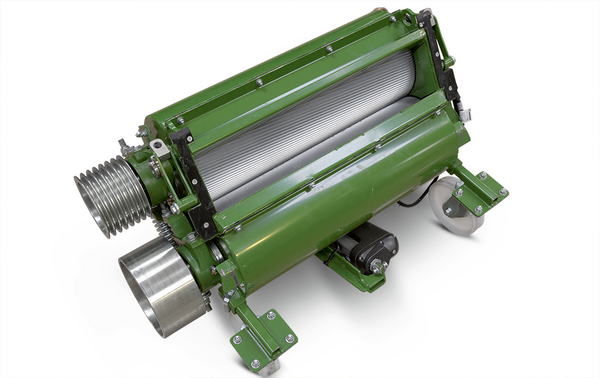
With the new OptiMaxx 250, KRONE presents a roller conditioner that off ers an even higher performance for the BiG X 680, 780, 880, 1180 models. This new development stands out for the following features:
- 250 mm diameter rollers have slanted teeth that give a unique shearing effect
- 10% longer rotors and a 7% higher rpm over the previous model.The greater length increases the friction
surface area and ensures an effective crop intake, intensive conditioning and optimum cracking results - Bigger and stronger springsapply a consistently high pressure on the crops
- The two rollers in the assembly have different numbers of teeth:
- 105/123 for medium and long chopping lengths
- 123/144 for short and medium chopping lengths
- A standard 30 % speed difference with a 40 % of 50 % differential being an option for intensive fracturing and optimum cracking results
- BusaCLAD-Special coating technology as an option for maximum service life
- Optional temperature sensors are available on the roller bearings for measuring the temperature and transmitting the readings to the operator terminal for maximum reliability and peace of mind.
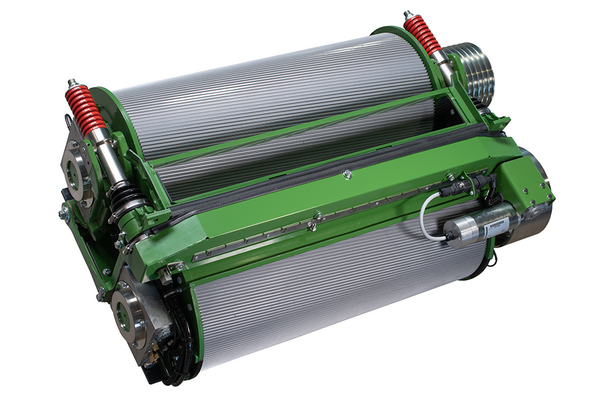
The two roller conditioners OptiMaxx 250 and 305 (left) are controlled by a massive and powerful spring assembly which applies a consistently high pressure on the crop and hence intensive conditioning to grains and stovers.
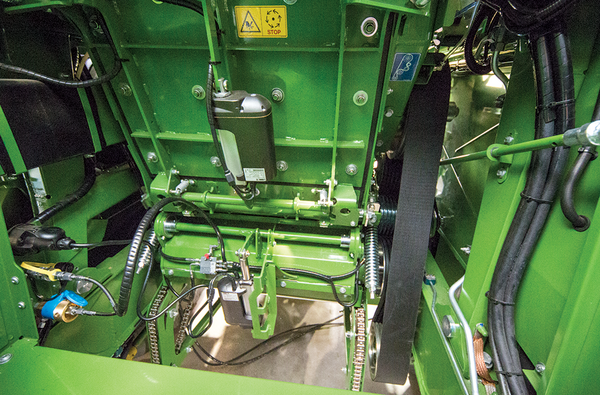
The gap between the rollers varies between 0.5 mm and 7.0 mm (0.3") and is adjusted steplessly by an electric motor from the cab.The current setting is shown on the display screen.
The two toothed rollers operate at a 30% speed difference. This standard difference can now increase to 40-50% to deliver 100% conditioning and fracturing of long chops as produced by OptiMaize XL.
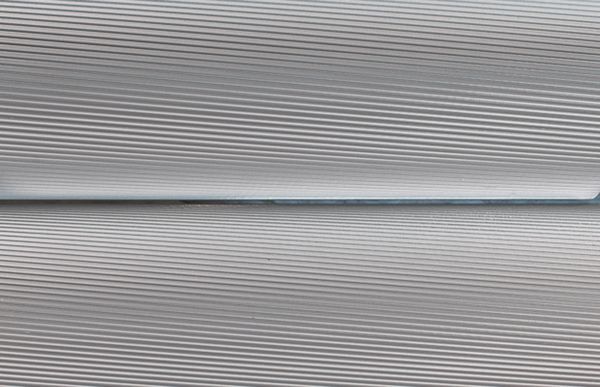
The new OptiMaxx roller conditioners have their teeth slanted at a 5° angle.This slant produces a clearly higher shearing effect and perfect conditioning of the crop which receives a very intensive treatment both length- and sideways.

- OptiMaize is a versatile and unique system
- Gearbox on the chopping drum for flexible use in short and long cuts
- Switching the drum speed takes a few minutes
- No downtime, no machine conversion, no up-front planning
Forming an integral part of the pulley, KRONE VariLOC is a gearbox that alters the speed of the chopping drum. By simply changing the drum speed from 1250 to 800 rpm using a standard open-end wrench, you can increase the chopping drum’s LOC range by up to 50%. This system allows operators to momentarily change from short to long chops and vice versa and meet different customer needs without a major changeover - this is the concept of OptiMaize. In conjunction with the roller conditioner with 105/123 teeth or with the disc conditioner, this technology turns the BiG X into a real all-round forage harvester that offers its owner and user maximum flexibility.

The KRONE VariLOC is available for the MaxFlow drums with 28 and 36 blades. VariLOC is a mechanical gearbox that allows the MaxFlow chopping drum to produce the full range of chop lengths (OptiMaize S-XL) with 28 or 36 blades.
The KRONE VariLOC is available for the KRONE MaxFlow drums with 28 and 36 blades. VariLOC is a mechanical gearbox that allows the MaxFlow chopping drum to produce the full range of chop lengths (OptiMaize S-XL) with 28 or 36 blades.

The KRONE VariLOC increases the cutting lengths that are available from the MaxFlow chopping drums with 28 and 36 blades. For the 36-blade drum it increases the range by 50% from 3-17 mm to 3-24 mm. For the 28-blade drum it increases the range by 45%, which means from 4-22 mm to 4-30 mm. This allows operators to adjust the chop length flexibly as the
application changes.
The KRONE VariLOC increases the cutting lengths that are available from the MaxFlow chopping drums with 28 and 36 blades. For the 36-blade chopping drum it increases the range by 50 % from 3 – 17 mm to 3 – 24 mm. For the 28-blade drum it increases the range by 45 %, which means from 4 – 22 mm to 4 – 30 mm. This allows operators to adjust the chop length flexibly as the application changes.
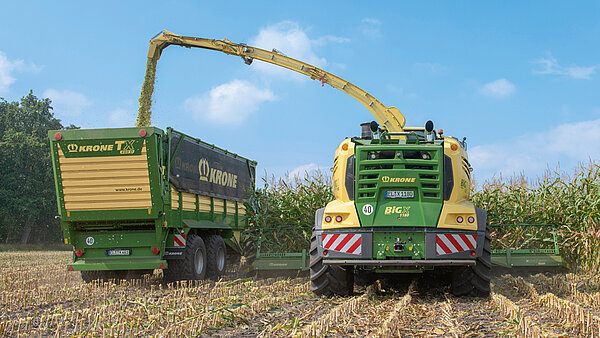
- Fast changeovers from grass to corn conditioning and vice versa
- A chain drive lowers the unit conveniently
- The changeover takes just a few minutes
- Fast and easy removal of the corn conditioner
VariQuick is the system that allows operators to converse BiG X very quickly from maize to grass. A chain drive (electric option) moves the corn conditioner out of or into the crop flow. If the corn conditioner is not used for longer periods of time, you can lower it and remove it from the machine by pulling it out to the side.
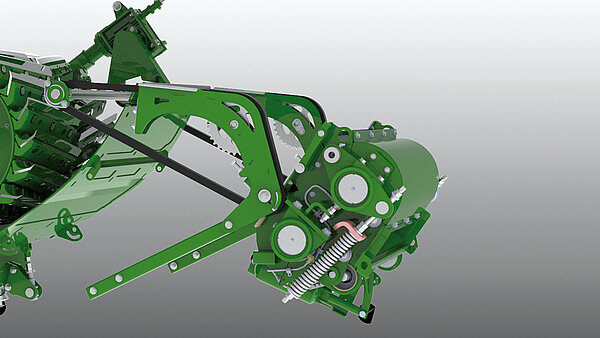
If the corn conditioner is not used for an extended period of time, you can lower it with the help of the chain drive and then remove it.
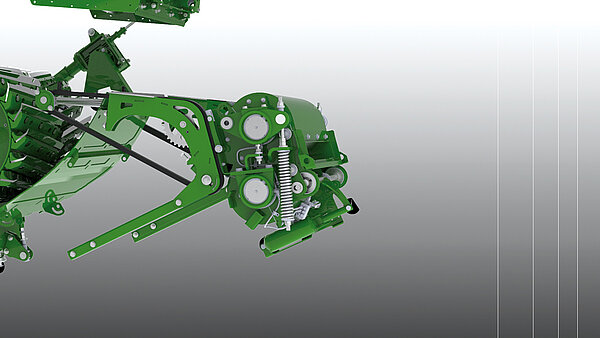
The chain drive moves the corn conditioner out of the crop flow and into its parking position so work can temporarily continue in grass without any major changeover.
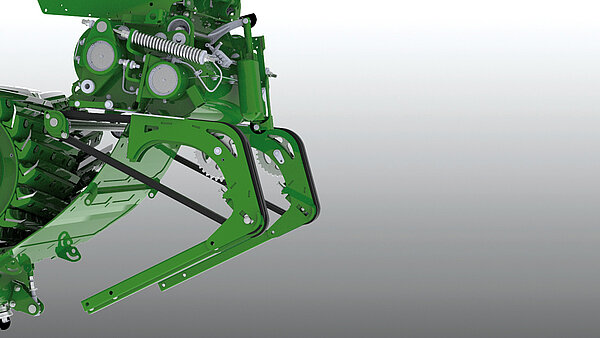
In this position, the crop flows through the corn conditioner. This way, the conditioner can subject the kernels to intensive treatment to make the nutrients available.
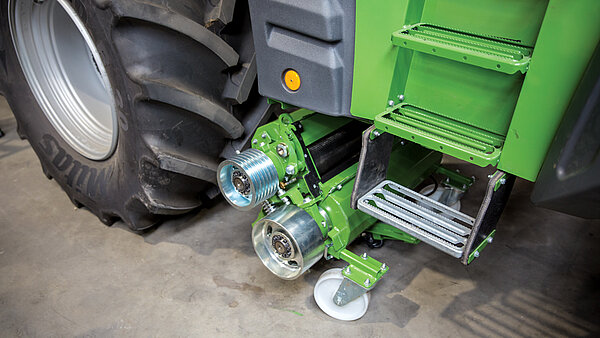
After the transport wheels are fitted without tools, the corn conditioner pulls out to the side and is conveniently rolled to the shed.
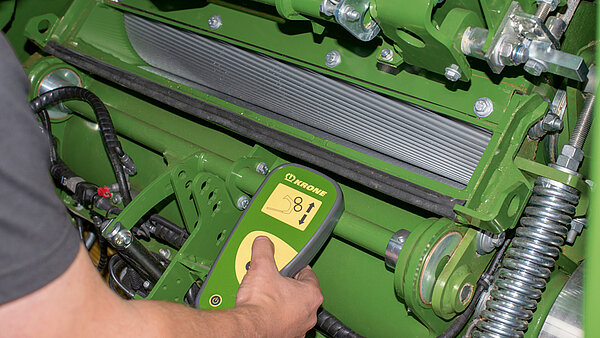
Change from maize to grass or from whole crop silage to grass on the move – either using a chain drive with crank handle or an electric motor as an option. This allows BiG X to change from maize to grass or from whole crop silage to grass flexibility and quickly.
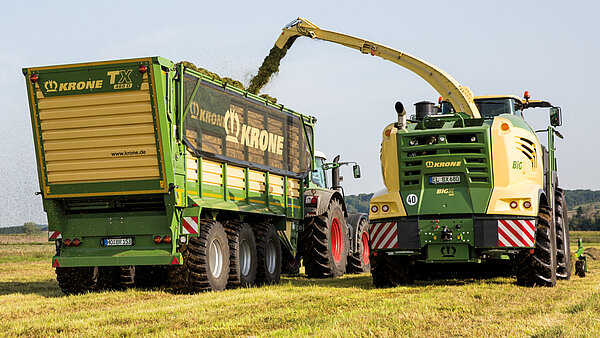
- Consistently smooth performance despite inconsistent crop flows
- Extremely smooth running – also in lumpy swaths
- High throughputs
- Top quality chop
- Operator comfort to perfection
KRONE VariStream comprises a spring-loaded floor beneath the chopping drum and a spring-loaded back plate in the crop accelerator housing.The system ensures blockage-free and smooth operation, even in varying volumes of crop. The technology allows operators to utilise the forager to its limit and use less fuel per hour.
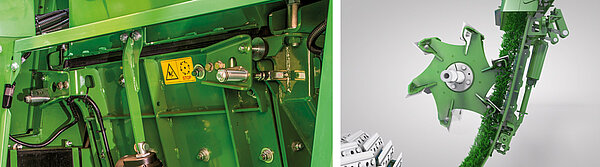
The spring-loaded backplate on the crop accelerator ensures maximum throws and targeted fills in all conditions.
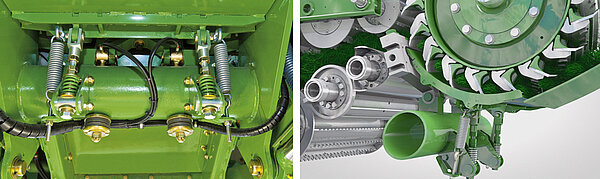
The spring-loaded chopping drum floor is connected to the anvil of the counterblade at the front. As these are readjusted, the gap between the blades and floor does not change. So any movement of the spring-loaded chopping drum floor that compensates for an inconsistency in the crop flow will not affect the quality of chop.
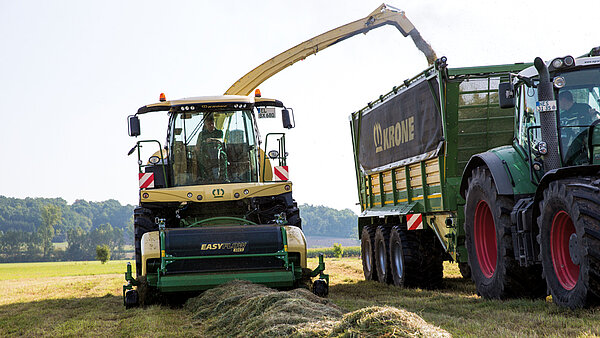
Lumps in uneven swaths absorb operator attention, reduce the overall performance level and can cause blockages. On BiG X, the chopping drum floor and the accelerator backplate are both spring-loaded to move momentarily out of the crop flow when the volume surges temporarily. The flexible cross section helps reduce the load on the engine and the chopping assemblies, and makes for quieter running and higher outputs.
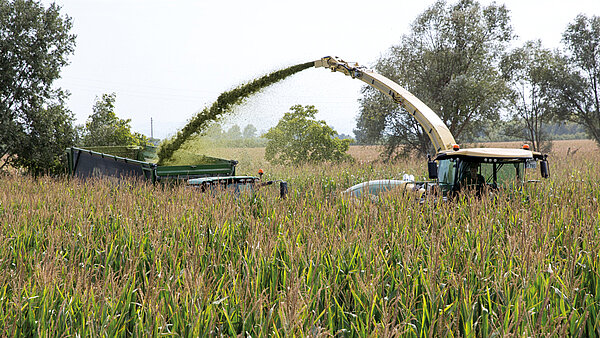
- Adjustable discharge distance from the cab as an option
- Tight crop stream even with a long crop throw
- The shorter the crop throw, the less power is needed
- Fills the transport wagon accurately without spillage
The crop throw is controlled from the cab by adjusting the door in the backplate on the crop accelerator.This way, operators can adjust the throw quickly to the current filling situation. As the accelerator needs less power to cover a short distance, the operator can free up engine output and use it for chopping and higher throughputs.
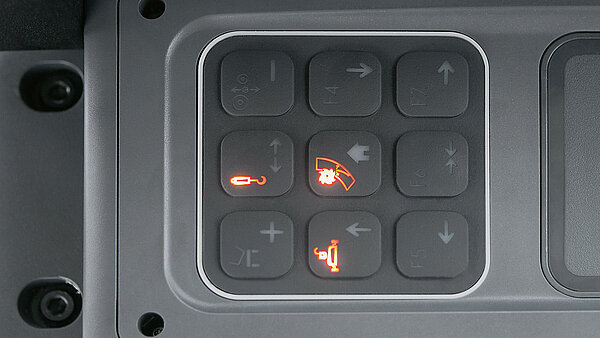
The additional crop throw control in the armrest offers operator comfort to the max.
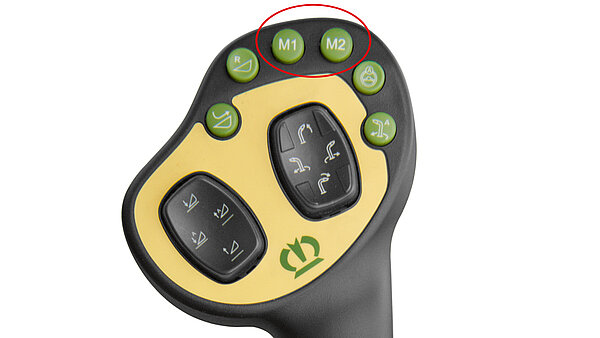
The throw is quickly changed on the joystick controls.
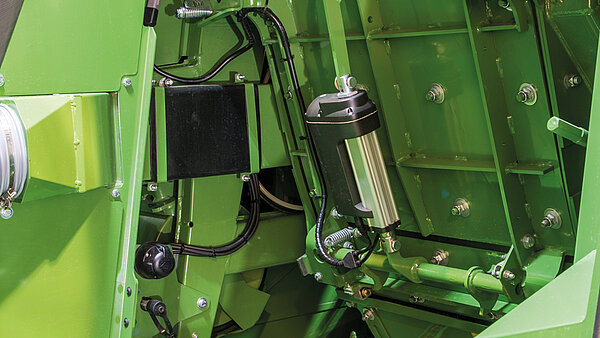
The hinged flap on the backplate of the accelerator is adjusted steplessly via an electric servomotor.
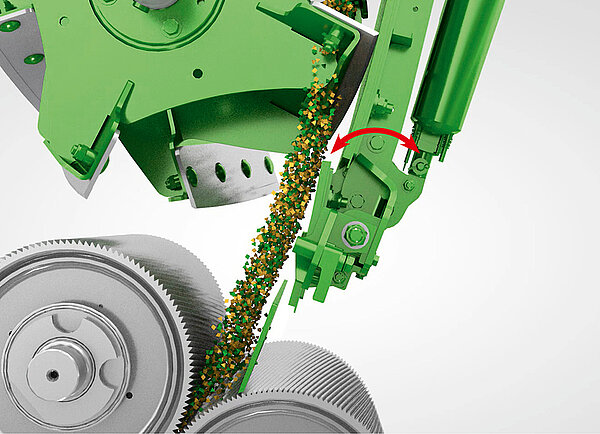
The crop throw is controlled via the hinged flap on the backplate of the accelerator. For a short throw, the flap moves out of the crop flow, so there is little contact between the crop and the accelerator. For a long throw, the flap moves into the crop flow, so there is more contact between the crop and the accelerator.
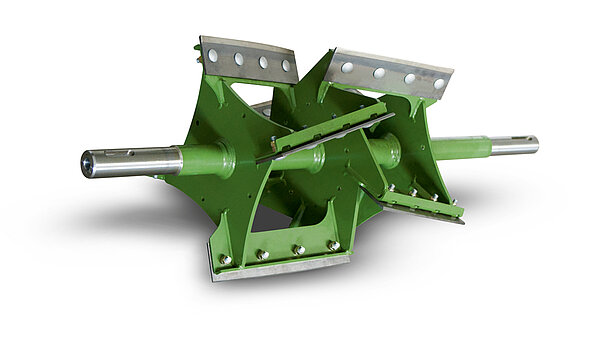
The paddles are designed for high crop output and guide the powerful crop fl ow towards the middle.
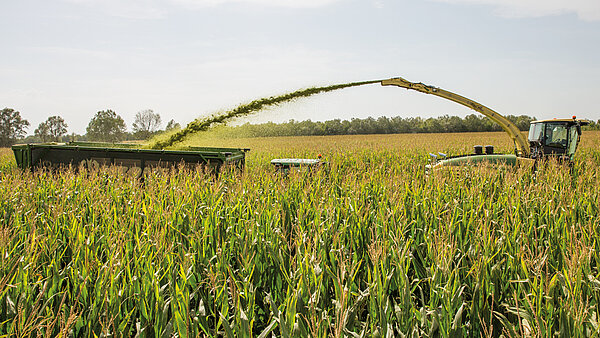
With the trailer following behind, the crop stream needs to be ejected from the spout at a higher speed. A strong, tight stream is needed to cover the long distance over the tractor to the trailer.
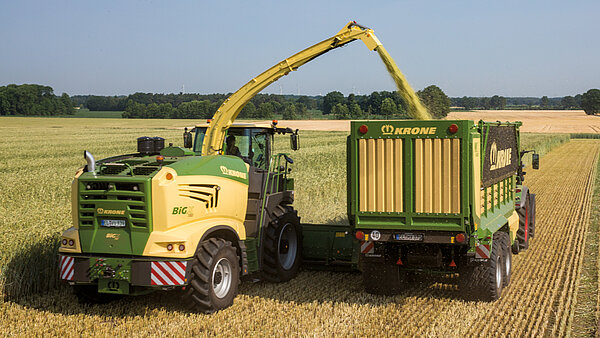
Filling trailers that are travelling alongside the forager does not require a powerful throw. Instead, in these situations engine output can be freed to boost the chopping capacity.
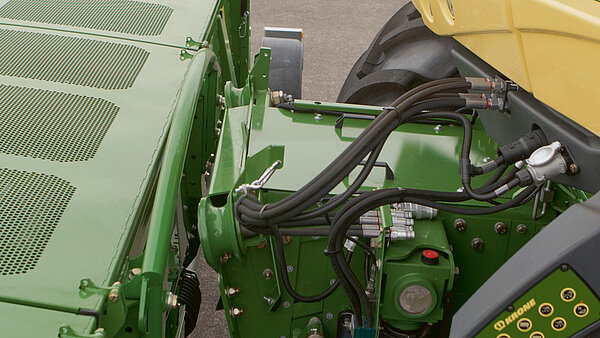
- Headers are swapped easily
- Convenient attachment and removal
- Very short set-up times
- Compact combination
- Maximum safety
The multi-coupler system of the BiG X allows operators to couple headers fast, easy and dependably from the seat, reducing changeover times when preparing for road travel or different crops. This way, more time is spent on productive work.
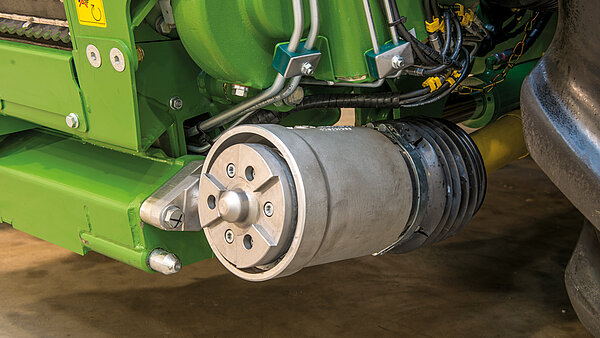
The multi-coupler couples the header automatically and reliably. The coupler is spring-loaded as an option. The frictional connection handles the highest loads.
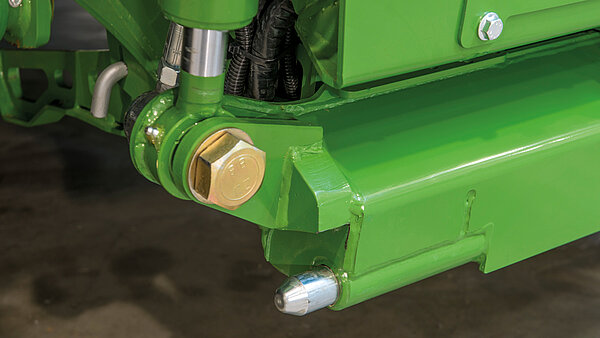
Pins down on the frame lock the header in place. These pins can be operated hydraulically as an option from the seat for convenient header attachment.
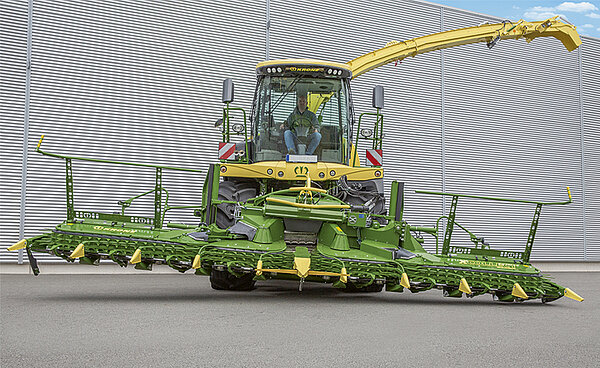
The header pivots laterally on the steel tubes that are trapped in the guide rolls. This type of attachment is easy and straightforward and makes for a large pivoting range.
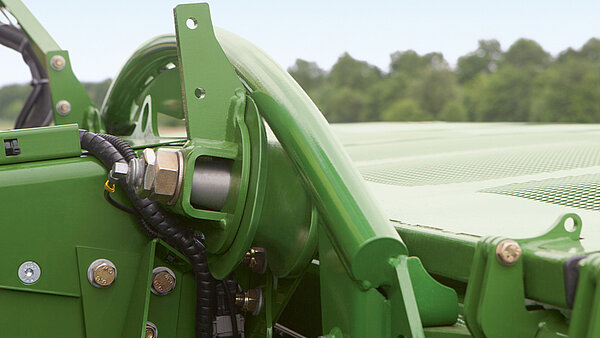
The two guide rolls on the base machine trap the curved round steel bracket on the header. Attaching the header to the base machine is as simple as that.
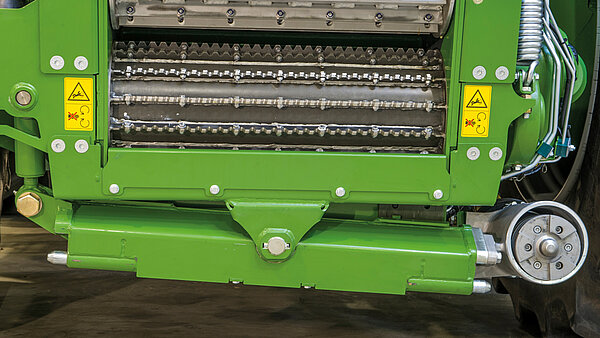
The header pivots freely to follow the ground contours as it suspends on a hydraulic cylinder on the side of the pivoting base which is made pressureless to give free pivoting.
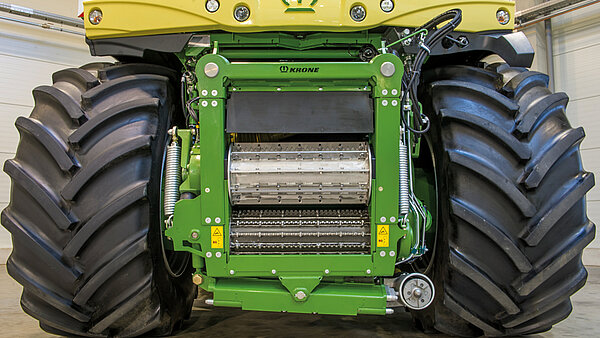
The robust intake system features guide rolls at the top and a supporting base at the bottom with locking pins (hydraulic as an option) which make attachment and removal easy and convenient and give accurate control to the header.
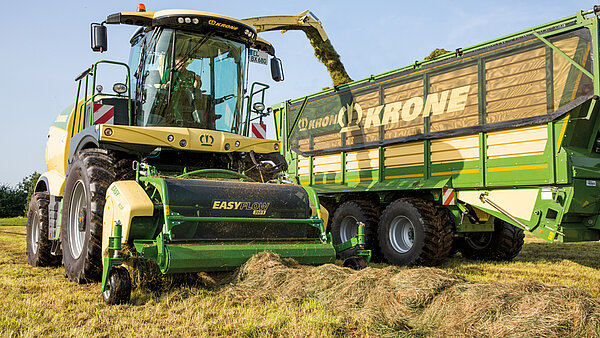
- Hard wearing pick-up without cam track, six rows of tines in W-arrangement
- Automatic pick-up speed adjustment to the current driving speed
- Gauge wheels on the sides and at the rear ensure perfect ground following
- Intake area lined with replaceable wear plates
- Quick header attachment thanks to curved round steel bracket
The camless EasyFlow 300 S and 380 S pick-ups have neither guide rollers nor cam tracks. Compared with conventional pick-ups, EasyFlow has up to 58% fewer moving parts, which makes it impressively smooth running, low-wear and therefore inexpensive in service and maintenance. EasyFlow operates 30% faster for cleaner gathering and increased productivity.
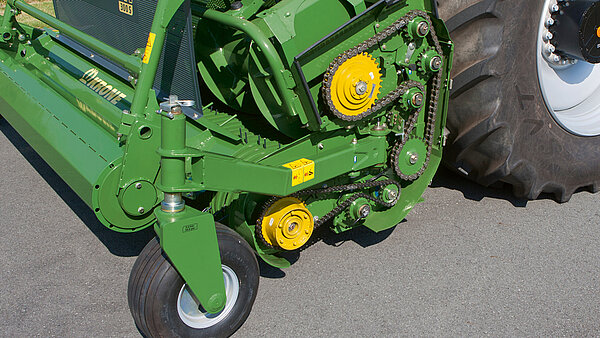
The drives for the pick-up and the auger are robust enough to handle even the toughest loads. They are fitted with automatic clutches for overload protection.
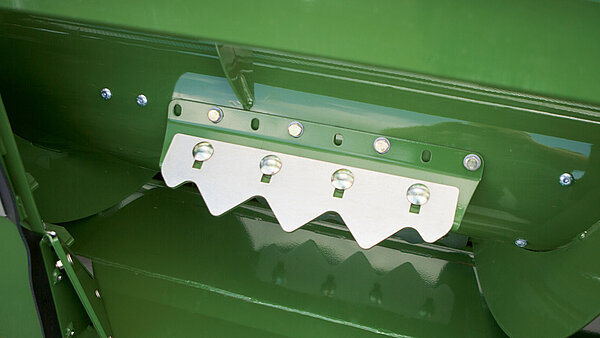
The serrated infeed plates can be set to one of two positions to provide different levels of aggressiveness, giving you the flexibility to respond to all conditions.
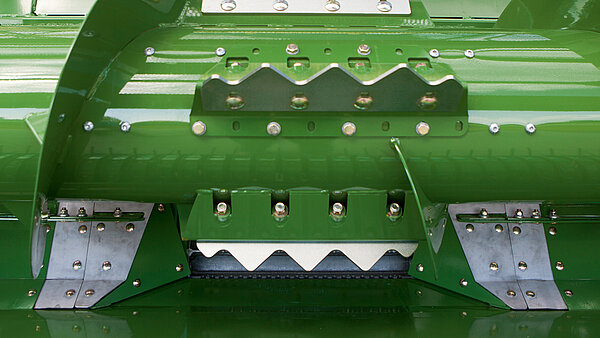
Replaceable wear plates increase the service life of the trough in the intake area.
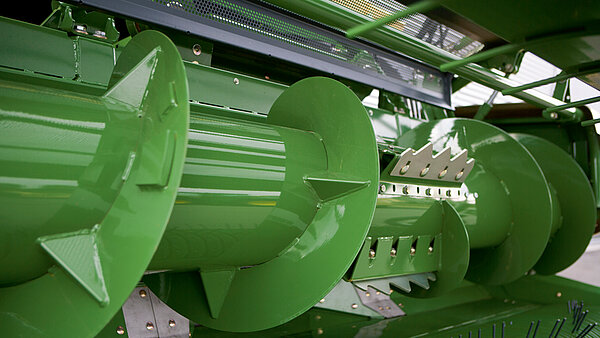
The large, 600 mm (2') diameter auger performs impressively even in dense, over-long crops.
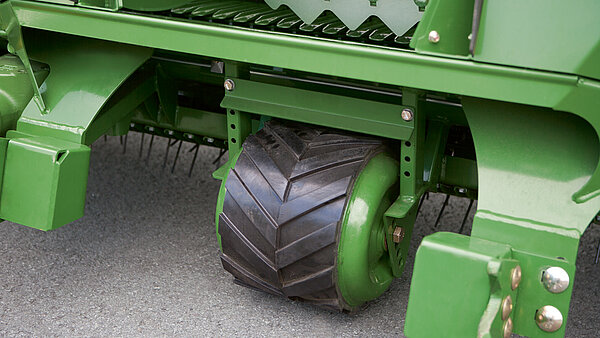
Two height-adjustable gauge wheels ensure optimum ground contouring on large work widths.
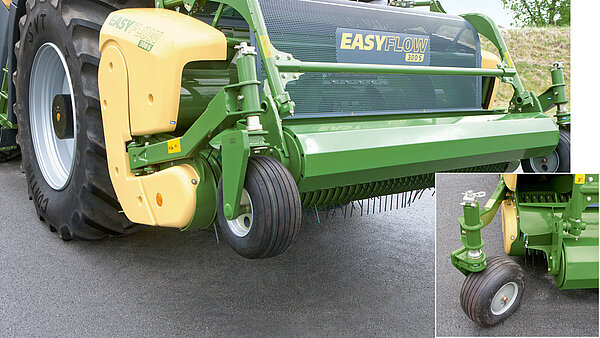
The unsteered and height-adjustable gauge wheels on the sides move hydraulically into transport position – simply upon a touch of button.

Its stepless height adjustment function and adjustable spring-loaded suspension allows the crop press roller to roll smoothly and adapt easily to varying windrow widths.
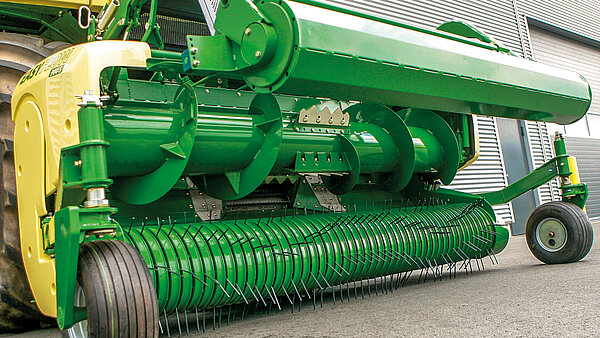
When the machine reverses the cross auger and the large crop press roller are raised automatically to give easy access to the intake system so foreign objects that were detected by the metal detector can be removed conveniently. When work is resumed, the press roller and the auger automatically return to their working position.

The standard-fit crop press roller is adjustable for a uniform crop flow also at high ground speeds.
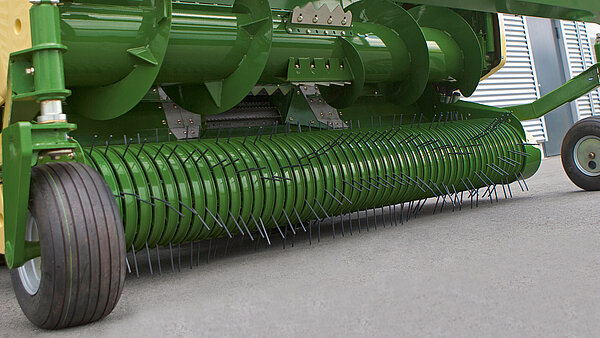
Six rows of double tines are arranged in a ‘W’ for a consistent and clean gathering of the crop even when the swath is not uniform.
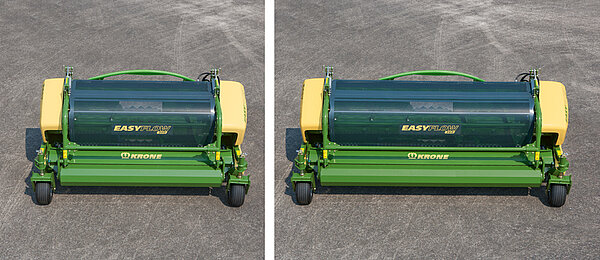
Working at widths of 3 m and 3.8 m, the EasyFlow pick-up on a BiG X gives the machine plenty of intake capacity. Depending on the swath width and your working speed, you can vary EasyFlow rpm steplessly from the cab or have it adjusted automatically to the current forward speed without the operator having to interfere. Its curved round steel bracket gives the Header the flexibility to pivot through a large angle and makes for easy attachment and removal.

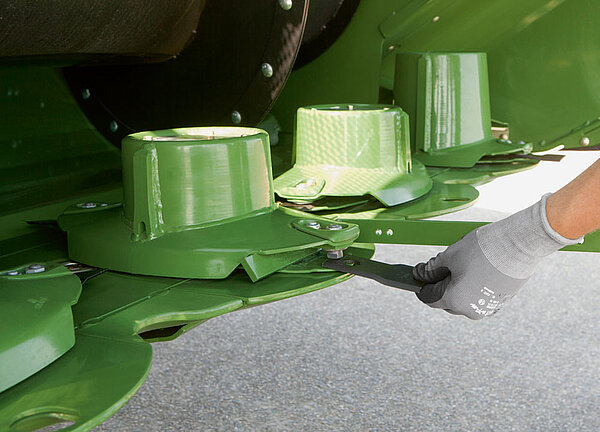
Quick-change blades are a must for many farmers and contractors, because this way they can replace blades quickly and easily on the site.
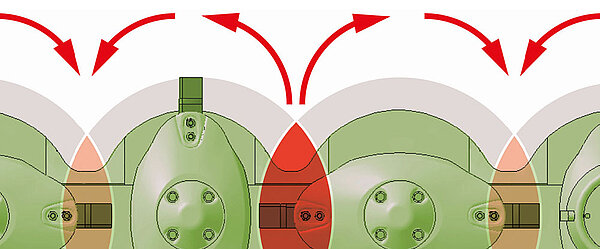
With some cutting discs turning in pairs towards each other and others turning away from each other, it was necessary to redesign the degree of blade overlap to ensure cleanest swaths. For a stripeless swath, we have therefore increased blade overlaps on the cutter blades turning outwards between the discs turning away from each other. In addition, the blades turning to the rear are set further apart to encourage a smooth flow of large volumes of crop.
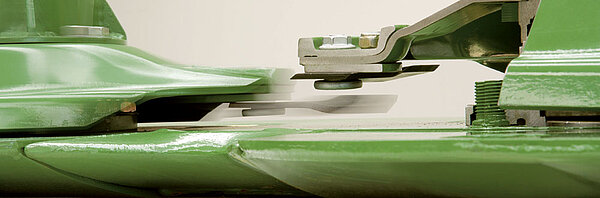
If the system is suddenly overloaded, the impact is not directed to the spur wheels in the cutterbar, instead the roll pins in the sprocket drive shaft shear off. The pinion shaft, which continues rotating, turns the cutting disc upwards via a lifting thread. moving it out of the risk zone and the orbit of the neighbouring discs. As a result, SafeCut prevents damage to the spur wheels and the neighbouring discs. The roll pins are replaced within a few minutes, saving costs and minimizing downtime.
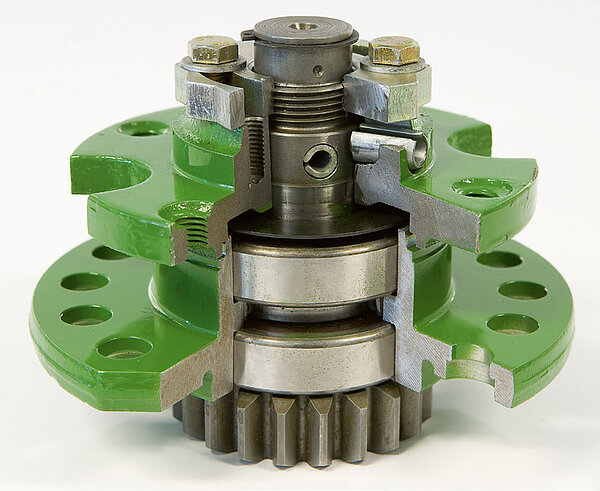
You know it too well – foreign objects can cause great damage and costly repairs. KRONE SafeCut offers a maximum of protection and peace of mind. A unique technology protects the cutting discs from foreign objects. The XDisc comes with SafeCut as standard.

KRONE XDisc is the versatile specialist mower for whole crop silage that cuts the crop cleanly and without wastage. The huge 900 mm diameter auger makes the unit enormously powerful and has no trouble picking up very long and bulky material.
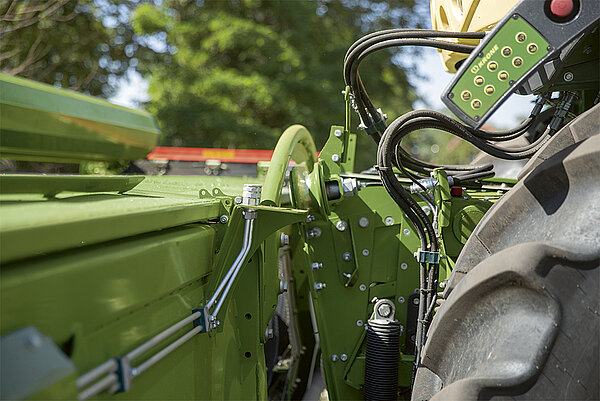
Fitting and removing the XDisc is quick and easy. With the rolls of the quick coupling, the harvester moves under the tubular frame of the XDisc. The spring-loaded quick coupling for the drive and the hydraulic locking system are available as options and increase the operator convenience.
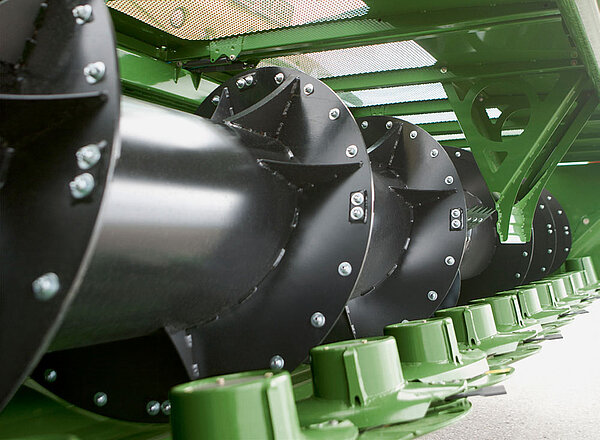
The powerful and massive 900 mm diameter feed auger works trouble-free even in dense and tall crops. It pivots freely and can be reversed. the auger coilings have replaceable Hardox steel wear plates.
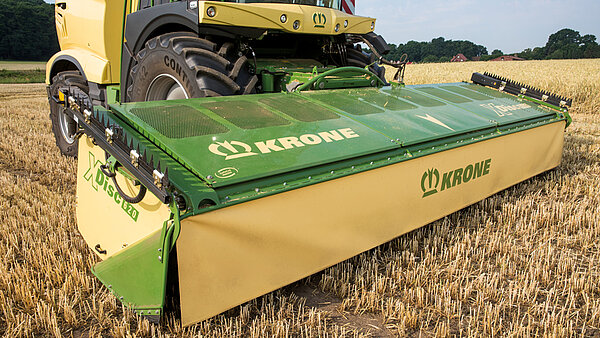
- Direct cut headers with 6.20 m or 7.10 m working width
- High throughput low power requirement
- KRONE EasyCut mower technology Proven the world over
- KRONE SafeCut Unique protection for cutting discs
- Powerful feed auger with replaceable HARDOX wear plates
Based on the proven KRONE
EasyCut mower
technology, the BiG X with the XDisc direct cut
headers can mow and chop whole crop silage
in one operation. SmartCut ensures high cutting
performance with the best cutting quality,
while SafeCut prevents damage from foreign
objects.
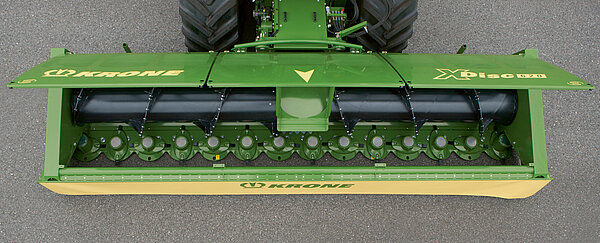
KRONE XDisc is the versatile specialist mower for whole crop silage that cuts the crop cleanly and without wastage. With its huge 900 mm diameter auger conveyor, the BiG X is extremely powerful and can easily pick up even long and bulky crops.
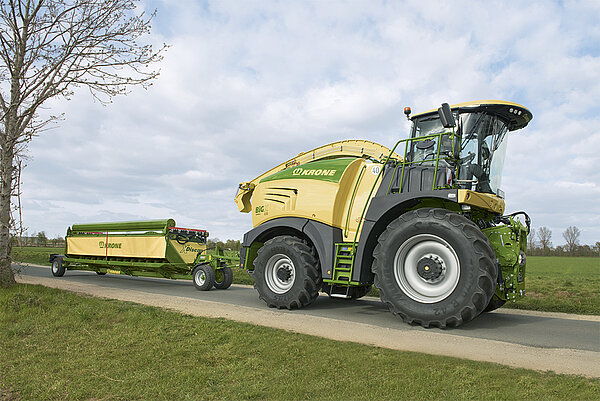
The direct cut header stores quickly and easily on the bespoke trailer with integral braking system for safe travel on public roads.
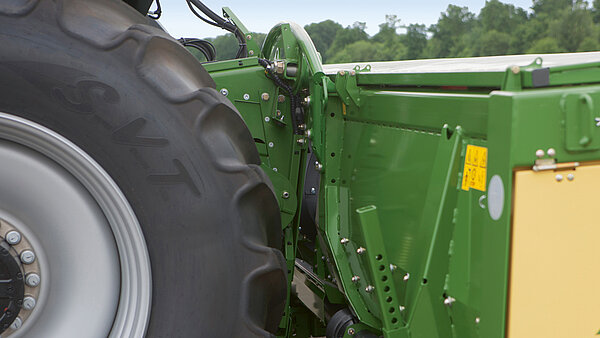
Fitting/removing the XDisc is quick and easy. The two guide rolls on the base machine trap the curved round steel bracket on the header. The spring-loaded quick driveline coupler and the hydraulic locking system are options.
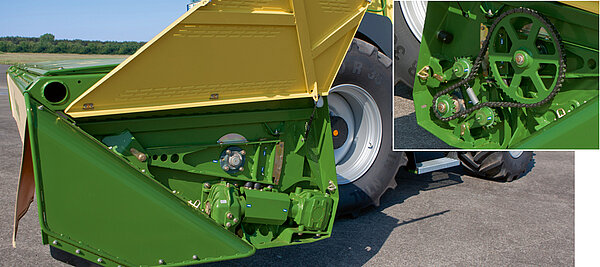
The cutterbar is driven by an angular gearbox, the auger is driven by a chain. The overrunning clutch inside the cutterbar allows the discs to come gradually to a standstill instead of stopping abruptly when the machine is shut off. The auger features overload protection in the form of a star ratchet.
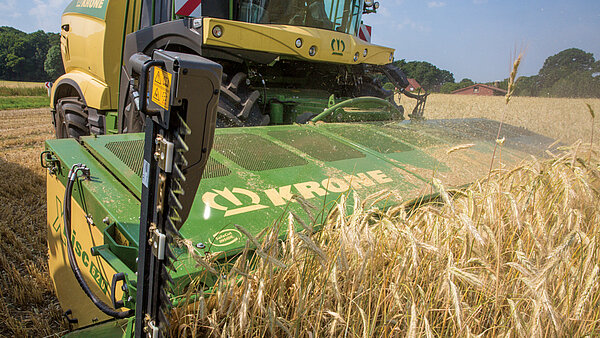
The direct cut header can be equipped with side knives as an option. The two knives are driven hydraulically and ensure loss-free harvesting of entangled crops like vetch rye mixes or whole crop silage mixes.
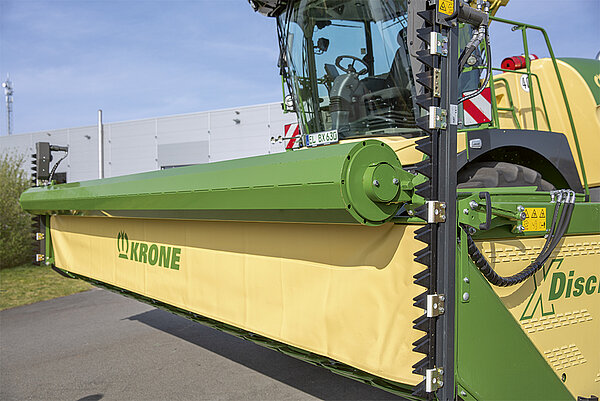
An optional crop press roller is available for the XDisc header which optimises the crop flow into the machine when harvesting high-yielding and tall stands. The roller enjoys blockage-free work even in extreme conditions
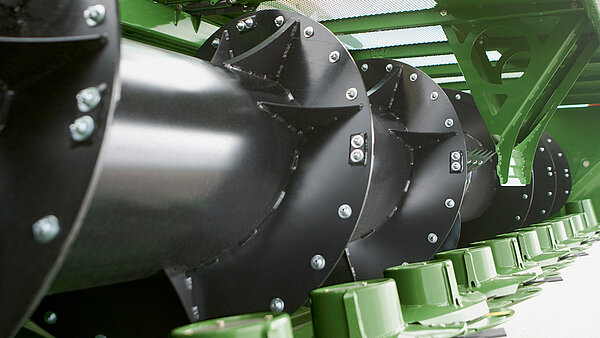
The huge 900 mm diameter feed auger gives BiG X enormous throughput capacities. The pivoting unit has a reversing mechanism and the auger flights have replaceable Hardox steel wear plates.
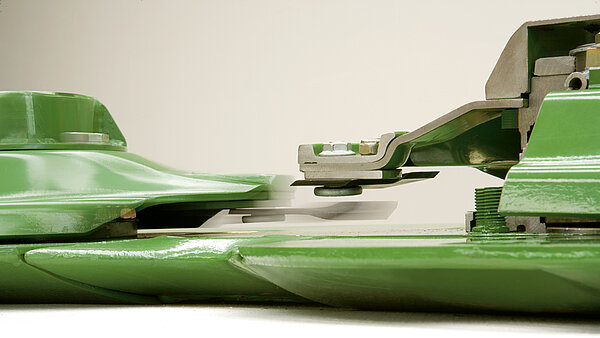
The SafeCut feature on the disc mower prevents a damaged disc from colliding with the blades on the neighbouring discs preventing damage to the spur gears. The XDisc comes with SafeCut as standard.
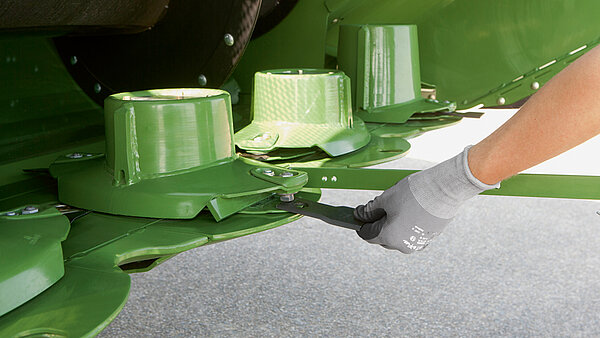
Quick-change blades are a must for many farmers and contractors, because this way they can replace blades quickly and easily on the site.
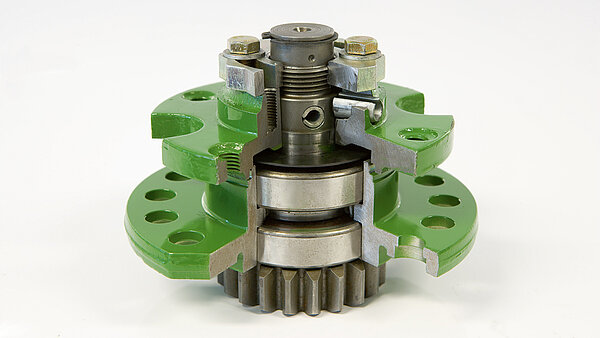
SafeCut centres on a roll pin that connects each disc to the gear and shears off upon impact with a foreign object.As a result the affected discs jacks up on a thread and out of the risk zone. The disc is not lost.
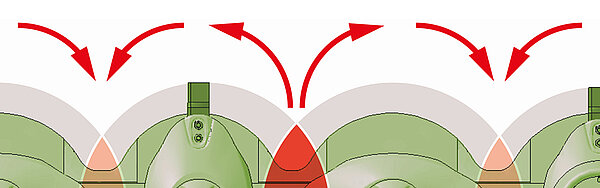
As the mower discs turn in both directions, the individual orbits must overlap precisely to ensure a clean cut. To reduce streaking cuts we have increased blade overlaps on the discs turning outwards. In addition, the blades turning to the rear are now further apart to promote smooth flows of large volumes of crop.
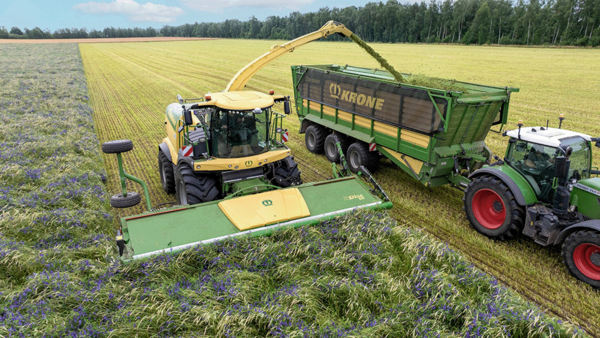
- 7.10 m working width for even greater throughput
- Clean cut thanks to EasyCut mower technology
- Optional: Side cutting blades can be conveniently swivelled out of the cabin
- Optional: Crop press roller unit for an even crop flow
- Optional: Integrated transport chassis for minimised setup times
The KRONE XDisc 710, a direct cut header with a working width of over 7 m and optional integrated transport chassis, sets new standards in terms of throughput and comfort. The 900 mm diameter feed auger can be adjusted three times in the base height, enabling optimum throughput. Optional side cutting blades are available which can be conveniently swivelled out of the cabin.

The XDisc 710 can be optionally equipped with side cutting blades which can be easily and conveniently swivelled up and down independently of each other hydraulically from the cabin of the forage harvester. This innovative and unique function offers an enormous advantage: efficient utilisation of the maximum working width prevents harvest losses from laterally protruding ears or climbing plant parts at the edge of the crop; this would occur if the cutting blade was not actively swivelled upwards.

To ensure a continuous crop flow even in dense and tall crops, the XDisc 710 can be optionally equipped with a crop press roller unit. This ensures an even crop flow to prevent blockages and enables smooth operation even under extreme conditions.

As there is no need to find a parking space for the transport wagon, there is also no need for awkward manoeuvring before harvesting begins. The XDisc 710 is easy to handle thanks to a swivelling single axle on the right next to the header adaptation and a folding drawbar with support jack on the left front side. By hydraulically swivelling the drawbar and axle, both chassis parts disappear behind the header during field work, leaving the working area clear
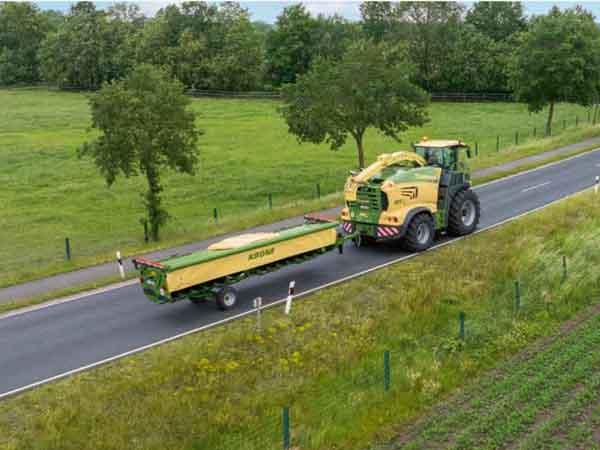
For transport on public roads, the chassis is swivelled under and the drawbar hydraulically next to the direct cut header. After the folding process, the direct cut header is attached to the tow coupling of the forage harvester. The integrated transport chassis replaces the additional transport wagon which was previously required, thereby making field changes considerably easier. Thanks to its innovative design, the direct cut header can be transported on the road safely and in compliance with the law as a stand-alone unit with an integrated lighting unit.

The drive chain for the auger conveyor is actively lubricated – this helps to minimise maintenance work on the direct cut header and to increase the service life of the drive chain

For a consistently clean cut in all conditions, the bearing pressure can be infinitely adjusted from the cabin of the forage harvester. The cutting height can be adjusted very easily and without tools using the centrally adjustable ground skids. If it is necessary to adjust the cutting angle, this is possible via a 3-way adjustable hole pattern on the round arch holding fixture.

The KRONE XDisc 710 impresses not only with its performance, but also with its outstanding accessibility and ease of maintenance. To change the blades, the guard cloth is folded up and the blades are replaced using the quick release fastener. The blades can be removed quickly and easily using the standard spare blade drawer. In addition, the centre hood can be easily swivelled upwards to allow free access to the intake rollers.

The large 900 mm diameter feed auger is designed for high throughputs. Its speed can be adjusted in three stages to the intake speed of the forage harvester, depending on the cutting length of the mown crop. In addition, the base height of the auger conveyor can be manually adjusted in three stages using eccentrics to allow the crops to pass through in the appropriate way. In addition, the free-moving auger conveyor can simply deflect upwards in the case of bulky crops.
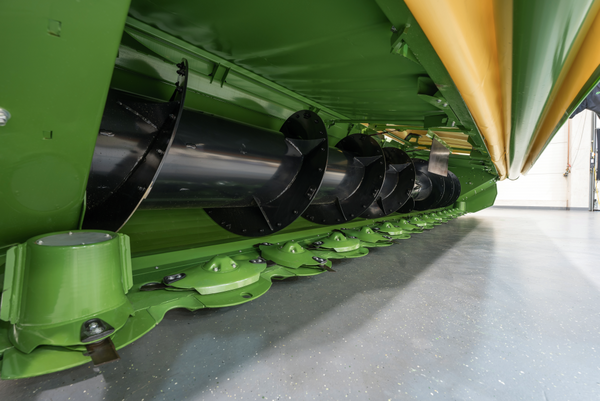
The powerful XDisc 710 is characterised by its exceptional robustness, enormous efficiency and high throughput. Two rigidly connected cutterbars are driven in a force-fit manner via universal shafts and angular gearboxes, starting from a central input gearbox. This guarantees an even cut even at maximum throughput, essential for outstanding chop quality. The drive train is specially designed for high input power and does not require an overload clutch. The auger conveyor is protected by a star ratchet clutch integrated into the gearbox and is driven by an actively lubricated chain drive, thereby ensuring a long service life

With its impressive working width of 7.10 m, the KRONE XDisc 710 direct cut header sets new standards in terms of performance. Thanks to its precise cut and perfect crop flow, it offers an extremely efficient solution for harvesting energy crops. With its integrated transport chassis, it also makes it quick and easy to move between locations, further increasing efficiency
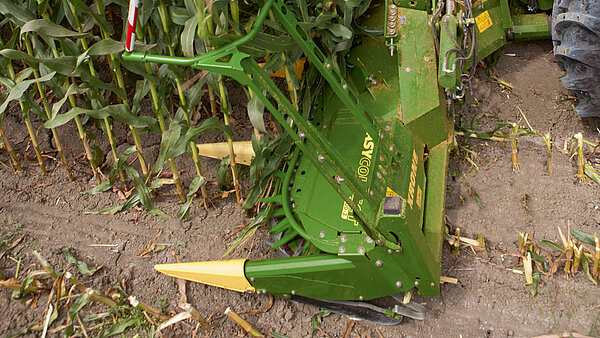
- Variable-row maize headers with 4.5m to 10.50m working widths
- Best quality of chop, fewer overlength fractions from linear crop feed
- Simple technology and low input power
- The central gearbox
- An extra running gear is available as an option for the two-piece EasyCollect model offering maximum road safety.
The variable-row EasyCollect header is a versatile unit that feeds the stalks lengthwise into the machine, which translates into an unsurpassed quality of chop. The unique collector principle from KRONE cuts labour costs and has proved its worth time and again the world over.
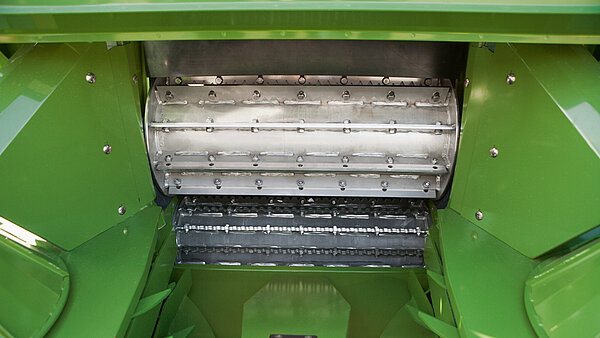
The dimensions of the EasyCollect intake system match the width of the intake rollers and ensure maximum throughput and top quality chops. The inline flow of the crop and the large intake width combine to provide a steady and uniform crop feed.
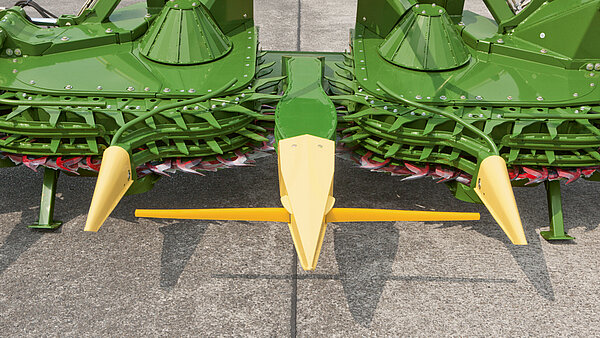
When Autopilot is enabled, the sensor arms on the central cone scan the distance between two crop rows. The KRONE BiG X is then automatically guided along the maize row. which helps reduce operator fatigue.
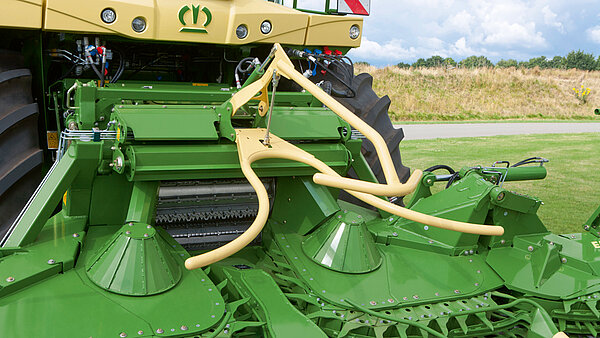
The crop divider adjusts its height hydraulically to different stalk lengths, so the round steel hoops at the top grab the stalks and pull them into the machine.
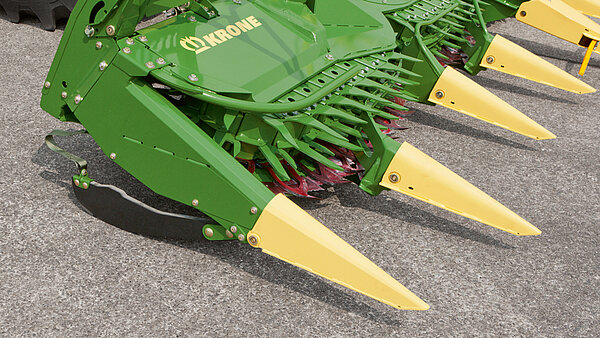
The ground tracers on either end of EasyCollect help maintain a uniform stubble height even in undulating terrain. They signal EasyCollect to follow the set depth in and across the direction of travel.
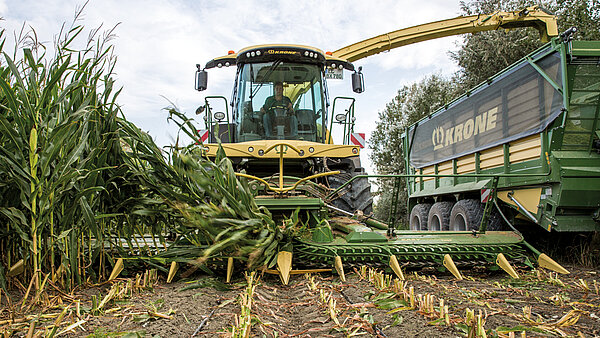
EasyCollect gathers the individual rows of maize firmly and feeds them to the middle of the header and into the machine. It is this tidy and lengthwise feed that accounts for the outstanding quality of the chop Also under difficult harvesting conditions as for example lodged maize, tidy gathering is guaranteed.
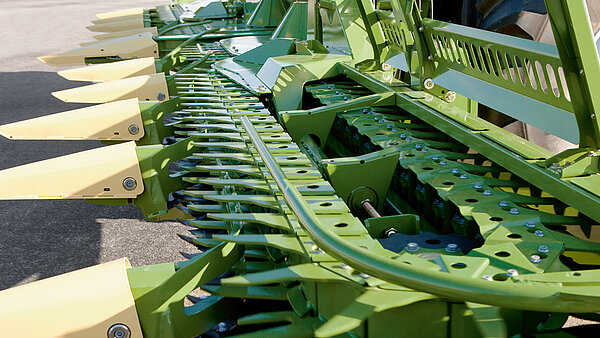
EasyCollect maize heads are built to a simple and modular design with endlessly moving collectors. This design leads to a much lighter weight, less maintenance and a long service life.
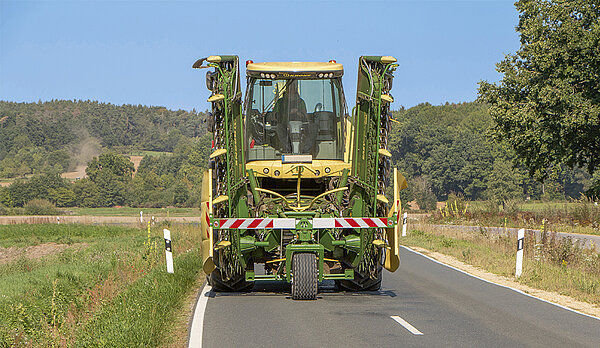
An additional running gear is available for the two-piece maize headers which shifts weight to the front axle for safer and even more convenient road travel. The running gear is conveniently locked and unlocked from the cab.
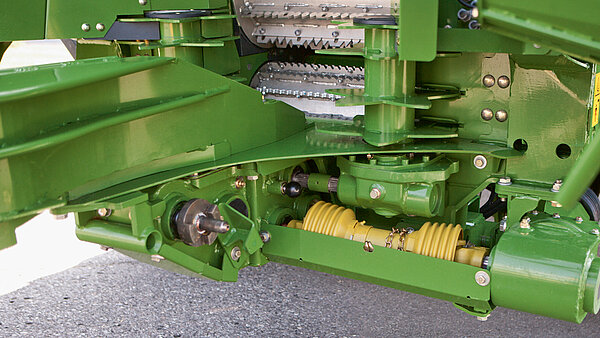
The drive power flows efficiently from the central gearbox down auto-coupling driveshafts to the folding collectors.
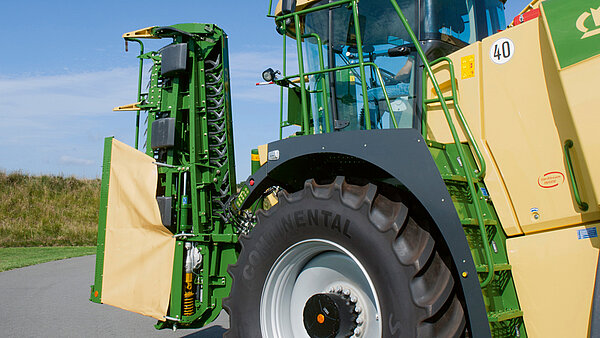
The 2-piece maize headers stand out for their straightforward design and uncluttered build. Its narrow transport width, its slim design and excellent visibility translate into safe travel between fields.

Rigid multi-section blades and endlessly moving blades combine to sever the stalks with scissor-like cuts. The blades are self-sharpening and easy to replace.
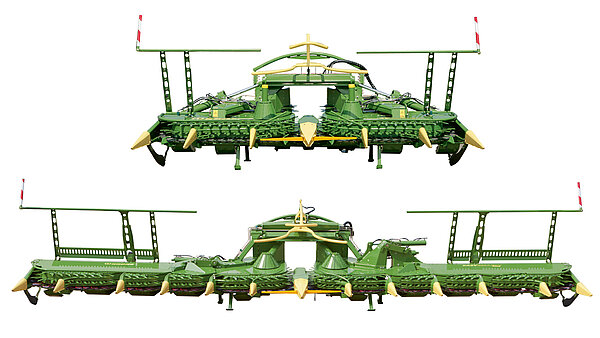
Working at widths of up to 10.5 m (34’5”), BiG X features the widest variable-row width header in the world. The endless collectors feed the stalks to the middle where they are turned through 90° and pulled in lengthwise.

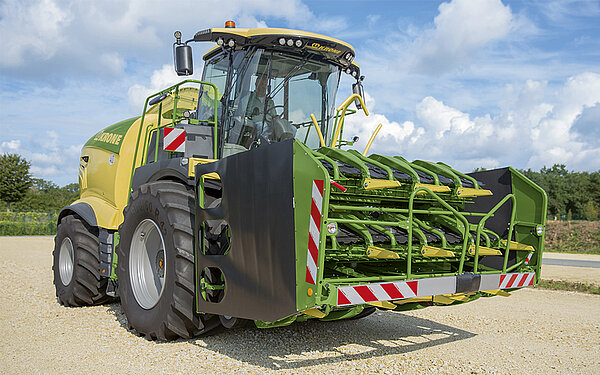
- Available work widths are 6 m, 7.5 m and 9 m
- Variable-row harvesting with rotating sickle discs
- Operates to the collector principle, splits the processes of cutting and feeding
- A smooth and soft cut eliminates vibrations and crop loss
- Operators adjust the cutting frequency infinitely variably to suit the prevailing harvest conditions
KRONE adds new XCollect maize headers to the long-standing and well-proven EasyCollect series. These units have two independent processes for cutting and conveying the crops. responding to customer demands to deal with diverse harvest conditions around the world.
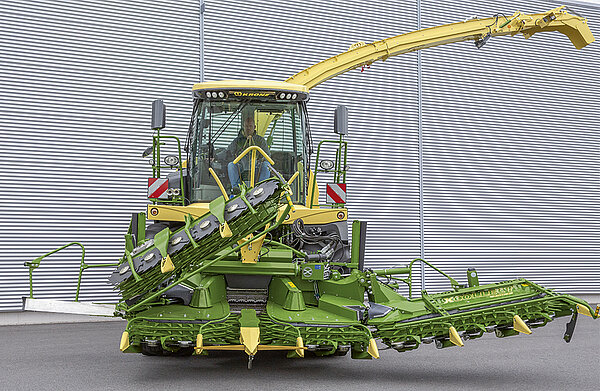
The wings on the three-piece XCollect headers fold up into their transport position. This design leads to a 3 m (9'10") transport width for the XCollect 600-3 and 750-3 and a 3.29 m (10'9") width for the XCollect 900-3 which have optimised hydraulic rams that lift and lower the wings even faster.
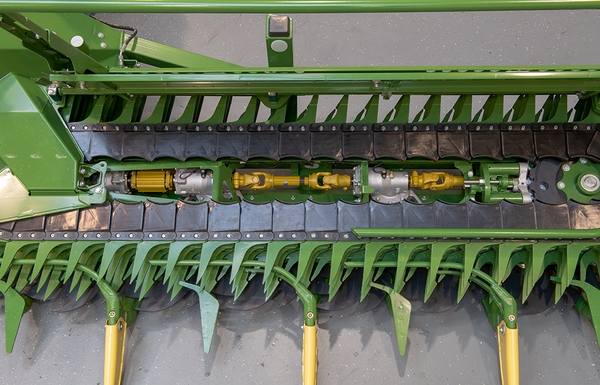
Star ratchet clutches protect the sickle disc driveline from overload. Speed sensors scan the speeds of two discs and send potential overload information to the operator terminal. In addition to this, a friction lining on each disc offers additional protection.
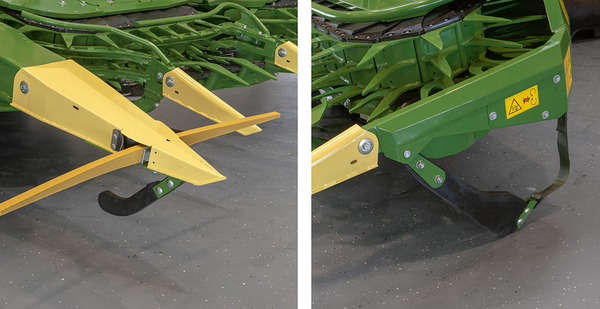
The header has three sensor skids, one in the middle and two out on the ends, for optimum contouringand clean cuts in undulating fields and for clean forage.
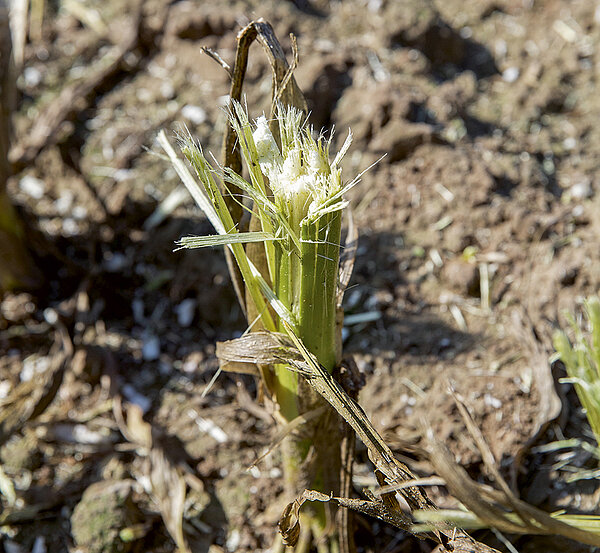
The high-speed sickle discs cut the stalks and defibrate the stubble for optimum breakdown.
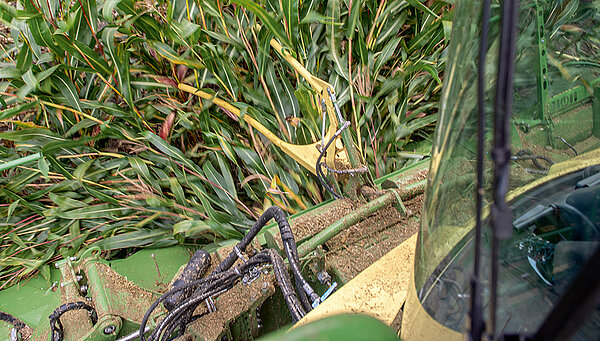
The well-proven collector feeds the stalks lengthwise to the chopping drum.It is this linear crop feed that enables precision chops and minimum overlengths.The variable collector speed is standard and ensures a consistently high quality of chop.
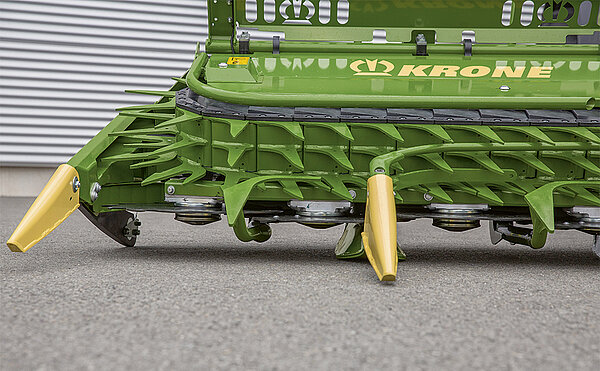
The sickle discs rotate on one plane, cutting the stalks without squeezing them. This technology minimizes vibration avoiding cob loss.
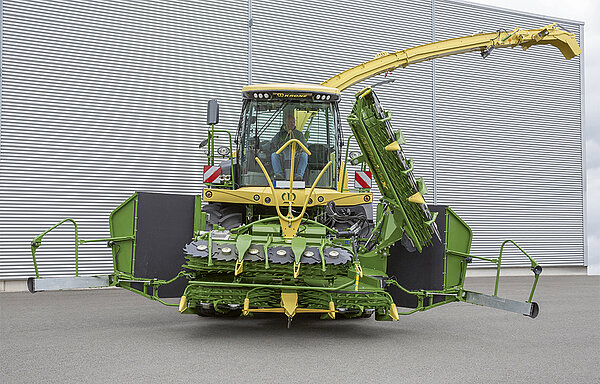
The ingenious guard for the maize header is an option that forms an integral part of the header. It moves automatically in and out of position when the header folds into road or work position. The operator just presses a button. No need to leave the cab. A very convenient solution that reduces changeover times and boosts productivity.
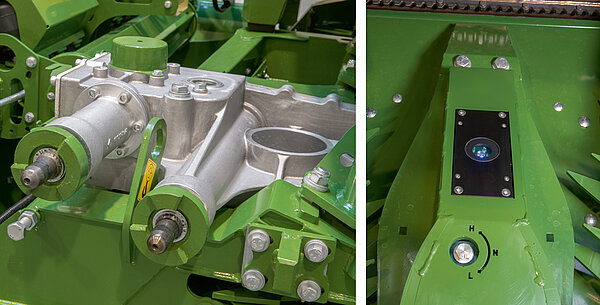
Operators can select one of two speeds to adjust the cutting frequency to the individual crop and harvest conditions.

The stalks are cut by high-rpm sickle discs which rotate on massive bolts that connect them to the drive train. The cut stalks are then fed to the chopper unit by endless collectors above the discs which ensure a uniform lengthwise feed.
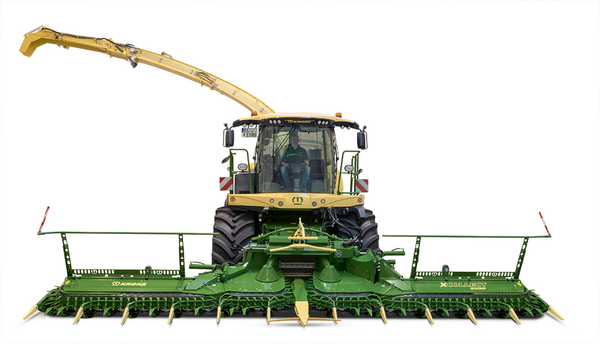
The XCollect maize header is available in three work widths: 600-3: 6 m (8 rows), 750-3: 7.5 m (10 rows) and 900-3: 9 m (12 rows)
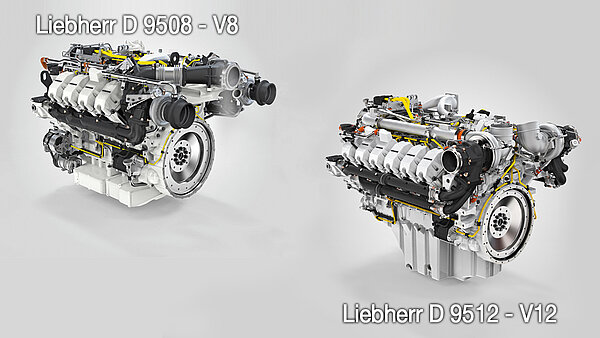
- 8- or 12-cylinder V-engines from Liebherr
- Compact V design for transverse mounting
- Final Tier 4 / Stage V compliant
- 687-1156 hp maximum continuous engine power
- High efficiency and quiet running
Advanced Common-Rail engine technology from Liebherr suggests superior outputs and fuel economy. The engines stand out for optimum torques, quiet running, superb fuel economy and high efficiencies.

As an option, operators can control the engine output with a touch of a button. Thanks to PowerSplit, they can operate the machine in the fuel-efficient Eco-Power mode whenever the full power is not needed. Vice versa, when the full power is needed, you simply switch to X-Power mode. The machine does this automatically and continuously variably depending on the current conditions. Another useful feature is the optional engine speed management which boosts efficiencies and fuel economy.

As an option, operators can control the engine output with a touch of a button. Thanks to PowerSplit, they can operate the machine in the fuel-efficient Eco-Power mode whenever the full power is not needed. Vice versa, when the full power is needed, you simply switch to X-Power mode. The machine does this automatically and continuously variably depending on the current conditions. Another useful feature is the optional engine speed management which boosts efficiencies and fuel economy.
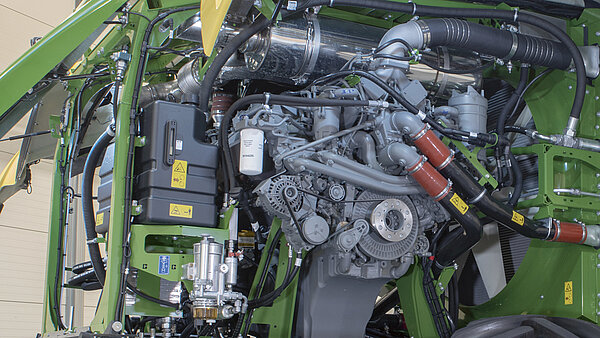
The engine is mounted sideways for optimum weight distribution. The power flows from the engine down a powerbelt and directly to the chopping and feeding components – a setup that ensures maximum efficiency.
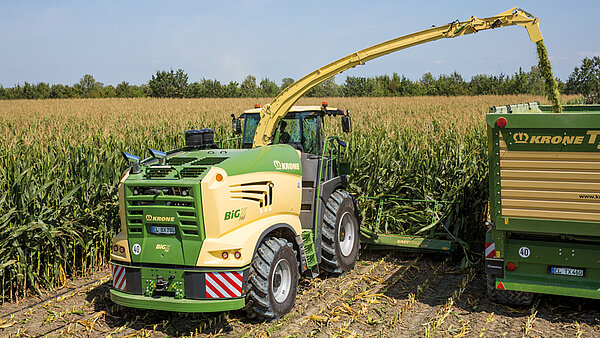
- Simple design
- An extra-strong poly V-belt transmits engine power to the crop assemblies
- Long service life
- Separate drive for the intake rollers and the headers: Rollers and headers are reversible if the chopping
drum suddenly stops - Separate and dependable driveline to the ground drive pump
The transversely mounted engine allows the chopping drum and the crop accelerator to take engine power directly off a powerbelt. The engine also drives the pumps for the intake rollers and the header and also the pump for the ground drive and the assemblies. The power flows through a power take-off gearbox which uses a multiplate clutch to engage the assemblies.
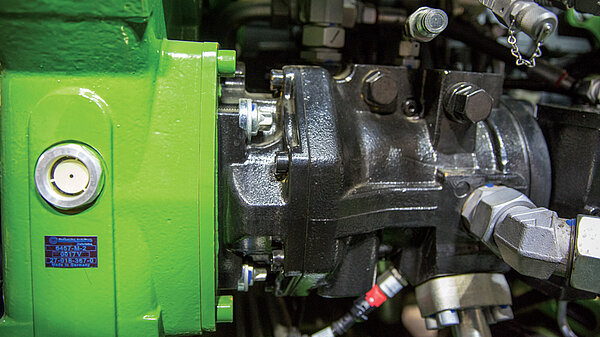
Courtesy of a hydro pump that is flange-mounted on the main gearbox, BiG X changes its ground speed infinitely variably. This is set either automatically or manually from the cab. The drive operates reliably and guarantees maximum reliability.
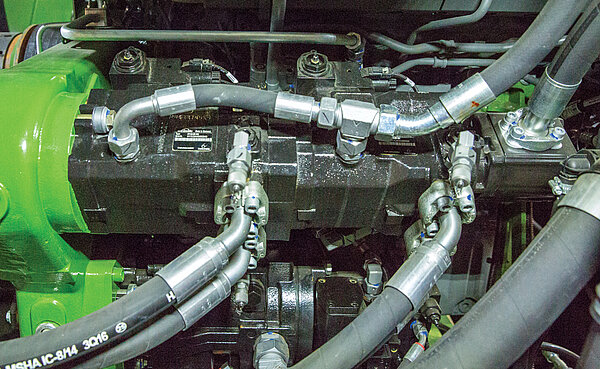
The header and intake system are driven by oil pumps. This concept allows operators to adjust the header and intake speeds steplessly – ideal for adjusting automatically to varying harvesting conditions.
1 Engine mounted sideways
2 Belt drive system
3 Crop accelerator
4 7-groove powerbelt to choppingdrum and accelerator
5 7-groove powerbelt to corn conditioner
6 Corn conditioner
7 Chopping drum
Power to the assemblies
The chopping drum and the accelerator are powered by a powerbelt that provides a direct connection to the transversely mounted engine. The accelerator shaft drives the poly V-belt for the corn conditioner on the other side. Slackening the powerbelt to the chopping drum reverses the intake system and the header.
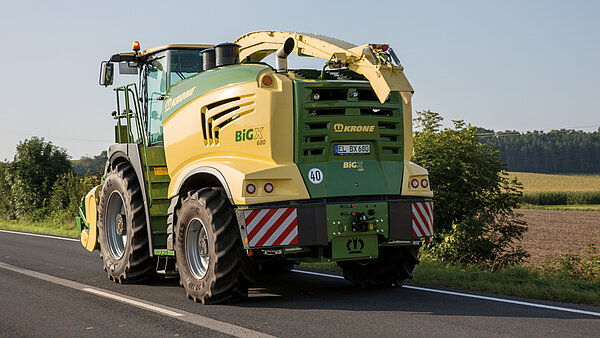
- Front-wheel drive is standard; four-wheel drive is an option
- Powerful wheel motors from Bosch-Rexroth
- Traction control with three travel modes
- High ground clearance powertrain
Wheel motors offer greater productivity and a higher level of automation and operator convenience. At the same time, this type of power train reduces maintenance and frees valuable space to fit a bigger and more powerful chopping assembly and move this further to the rear of the machine.
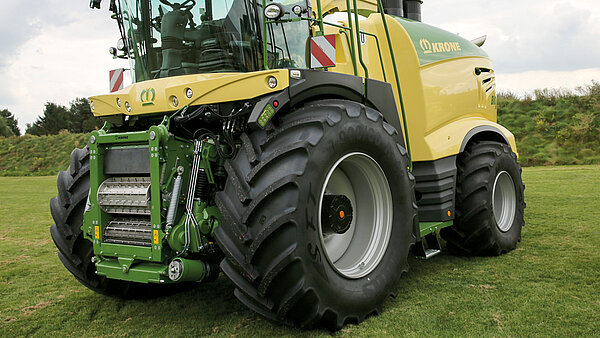
There is a choice of tyres available for BiG X. Large tyres offer plenty of ground clearance and reduce compaction. The BiG X 680, 780 and 880 can be fitted with up to 900/60 R 42 front tyres.
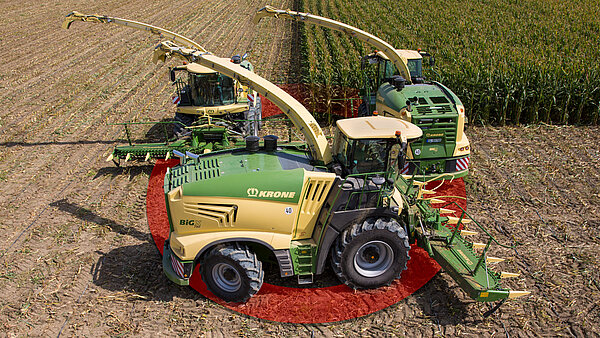
Using wheel motors increases the steering angle to a generous 50° for tightest turns and perfect match-ups after headland turns
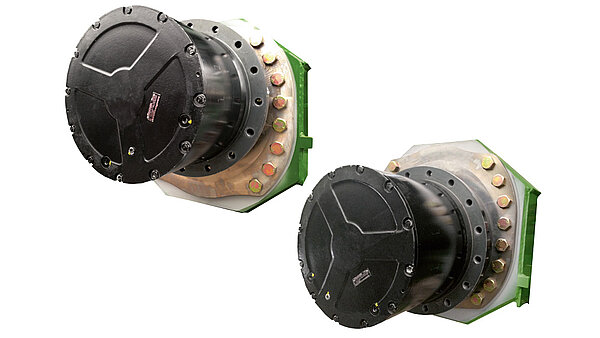
The wheel motors are mounted eccentrically on the front axle which allows you to fit small or large tires and still retain the position of the pick-up, the intake system and chopping drum floor relative to the downstream crop flow. This allows an optimum and consistent crop flow and increase ground clearance.
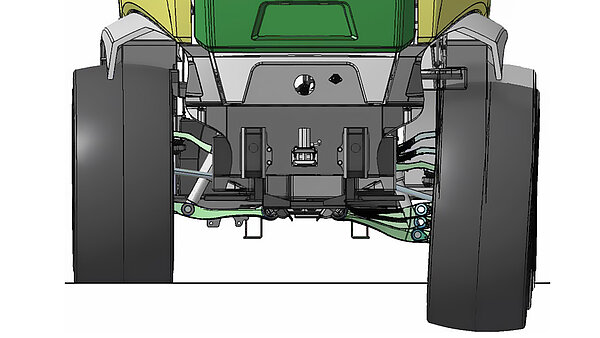
The independent wheel suspension system off ers plenty of room for steering so that even when clad with massive tyres BiG X remains a very nimble machine in undulating terrain. In addition, the suspended system provides maximum operator comfort.
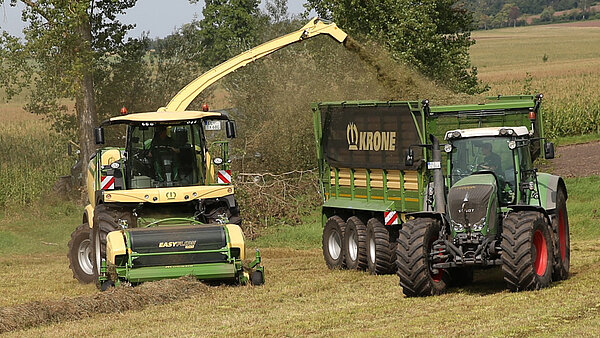
- Superb manoeuvrability from independent wheel suspension and wheel motors
- Sprung steering axle
- Height adjustable wheel motors
- Large choice of tyre options
Its hydrostatic wheel drive, its independent wheel suspension and its compact build
make BiG X a tremendously agile machine that gets into every corner and turns
elegantly on tight headlands, saving turnaround times and increasing productivity.
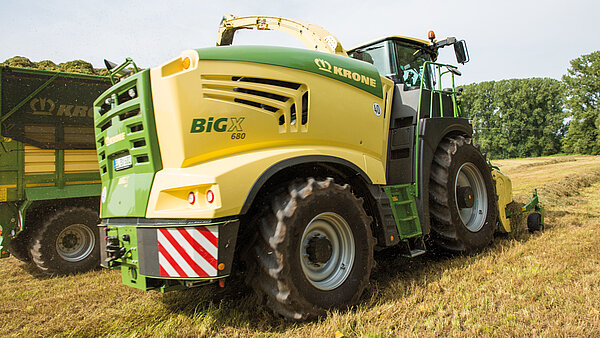
The operator decides which of the three travel modes to use. The mode that reduces wheel slip is usually selected when the focus is on protecting the sward. Maize foraging usually takes place in a mode that admits more wheel slip or even with traction control deactivated.
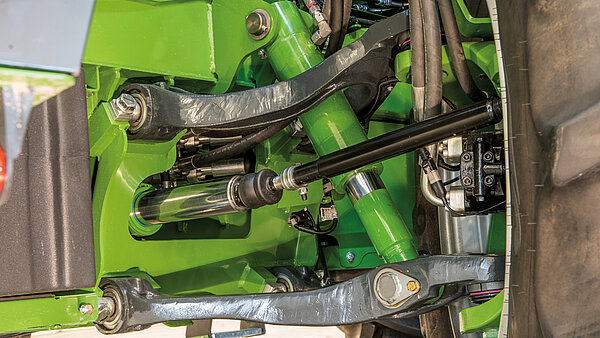
The steered axle on the BiG X comes with spring suspension as standard to ensure maximum operator comfort – both in the field and on the road.
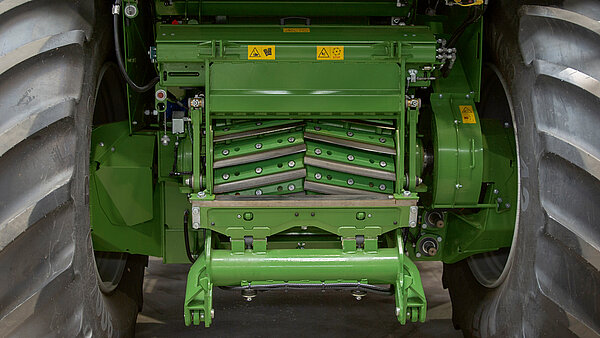
The use of hydraulic wheel motors results in a very generous ground clearance and creates room for a larger diameter chopping drum and also leads to a more even weight distribution.
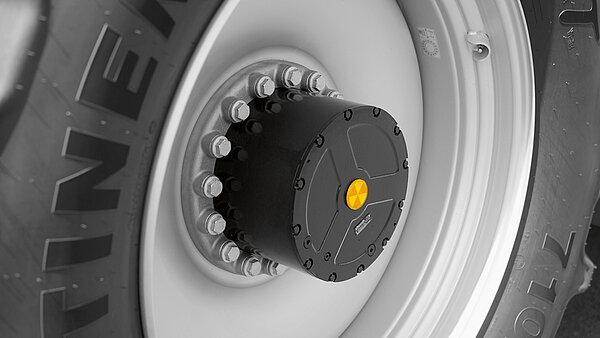
The wheel drives are planetary gearboxes from Bosch-Rexroth. These offer the advantage of distributing the load to several planetary wheels which are compact and enable high torques.
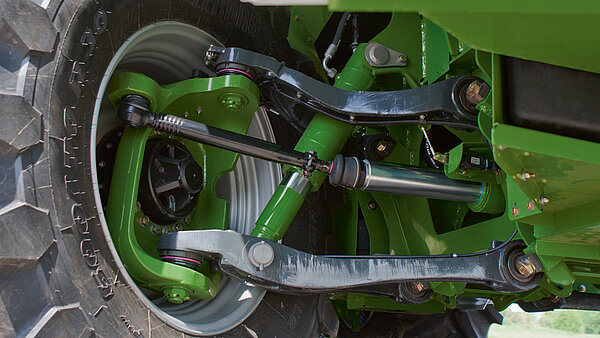
All BiG X machines have front-wheel drive as standard specification and have the wheel motors on the rear axle replaced by hubs.
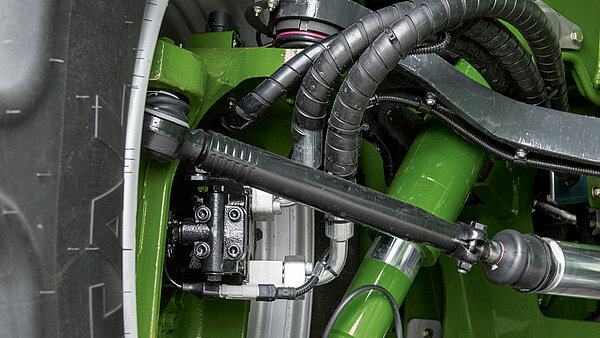
The BiG X 680 – 1180 are available with hydraulic all-wheel drive via wheel motors on request.
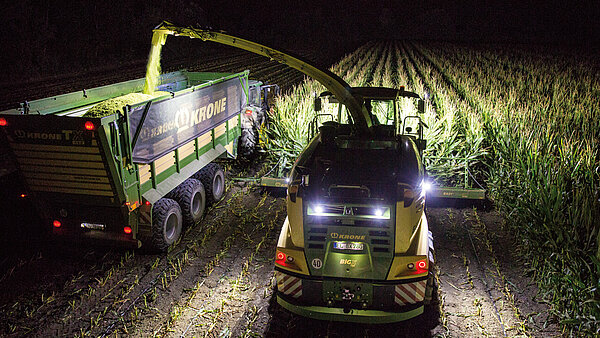
- LED lights for best visibility at night
- Optimum access to all service points
- Large storage compartment for tools
- Auto lubricator for more convenience
In the heat of harvest operators often work into the night.To ensure best visibility BiG X is equipped with a comprehensive light kit that turns night into day. Service and maintenance are made easy too thanks to wide opening side panels, an opening engine compartment cover, removable plastic mudguards and a ladder that swings out of the way to give easy access to all service points.
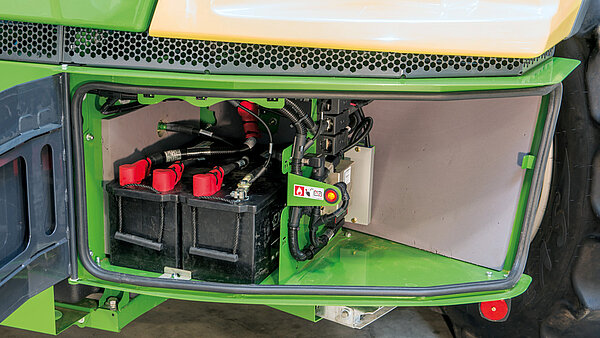
The batteries are stored in the storage space on the right side of the machine where they are in easy access.
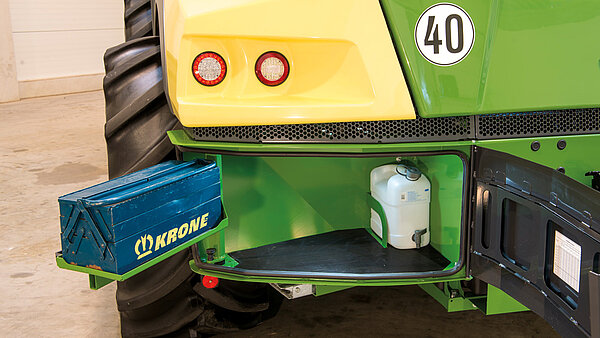
The nearside storage compartment at the rear boasts a pivoting table which accommodates the toolbox for convenient use.
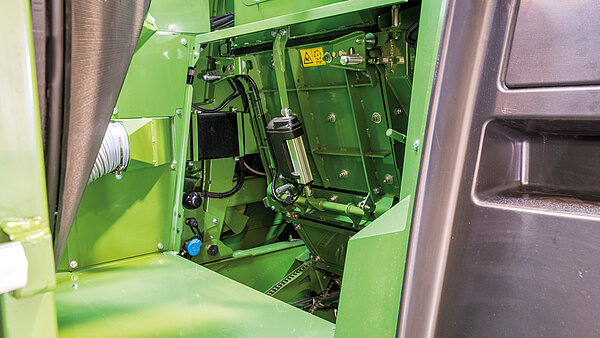
The space between the radiator screen and backplate of the crop accelerator provides excellent access to all elements in the crop flow system.
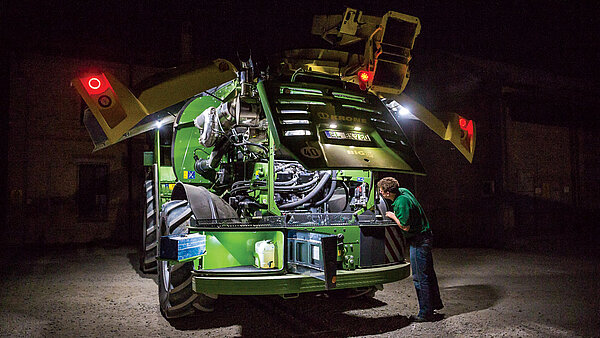
The hoods open wide and the rear mudguards give perfect access to all assemblies. LEDs are in place for easy service and maintenance even in poor light conditions.
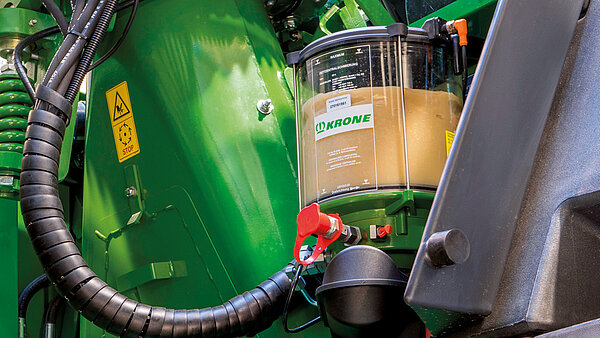
The auto lubricator and its large grease reservoir allow operators to spend less time servicing and maintaining the machine.
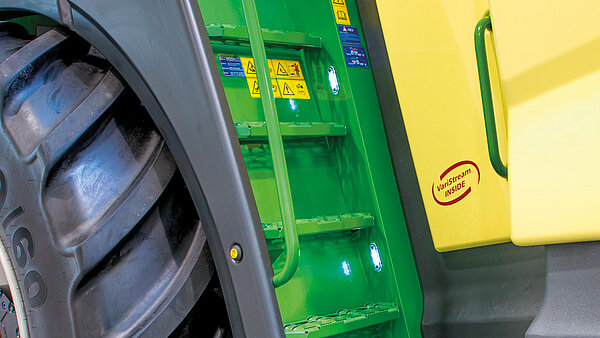
LED lights on the steps make access to the cab at night a safe climb.
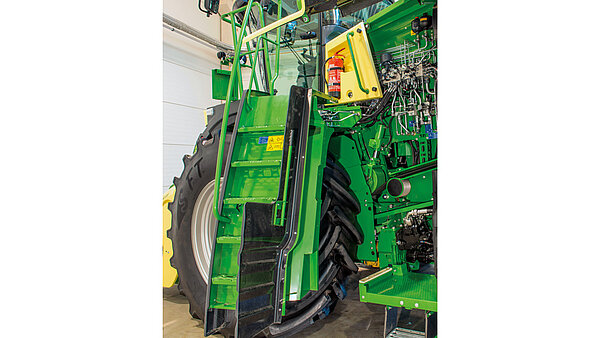
The access to the cab is easily moved out of the way to give convenient access to all nearside service points.
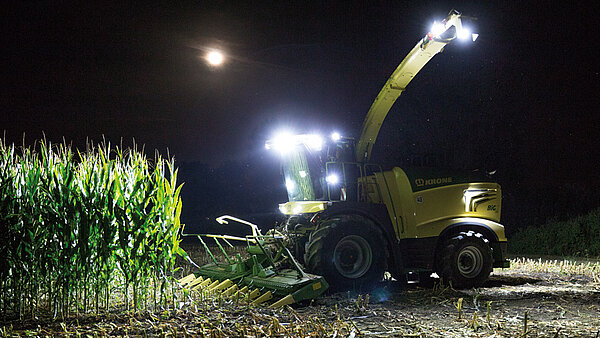
BiG X can take up to 23 optional LED work lights which make field work safe and effective even during those night shifts.
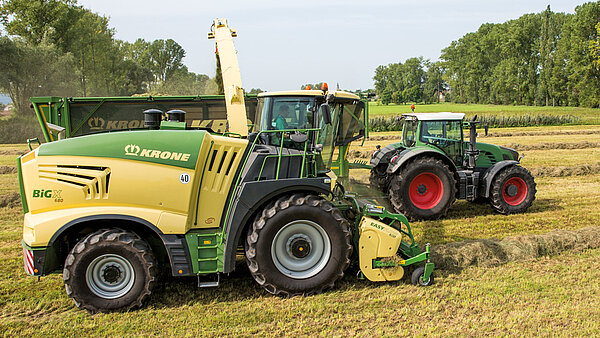
- Seven different tank systems are available for maximum flexibility
- Customers can opt for more fuel or more silage additives
- Integral silage additive applicator with small/large dose rates as an option
- Maximum fill capacities for long working days
A system of several tanks allows customers to specify the reservoirs on the machine to their needs – fuel, silage additive and water tanks can be added and configured in as many as seven different arrangements that meet individual needs around the world.

The dispenser for adding silage additives at high rates (0.5-7.5l/min) is integrated on the offside platform next to the cab. You can also use the nearside tank to store silage additives and increase the on-board volume to 505l. Two 13-litre silage additive dispenser for small dose rates (0.03-0.25l/min) can be integrated in the right wheel housing. In addition, it is possible to fit an external silage additive system. The silage additive can also be added relative to yields (option).
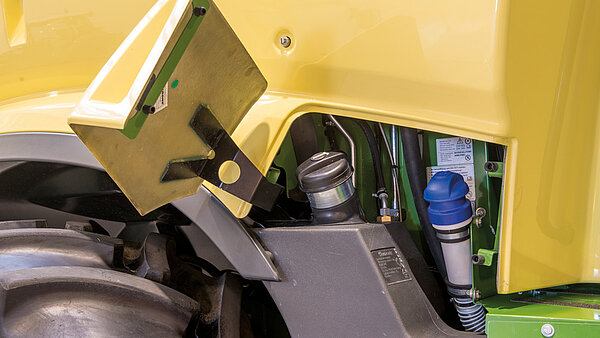
For example you can add a 150l urea solution tank to the 1500l or 1100l diesel fuel tank and a 275l or 505l silage additive unit. BiG X features a flexible system of tanks that offers customised solutions for individual machine applications.
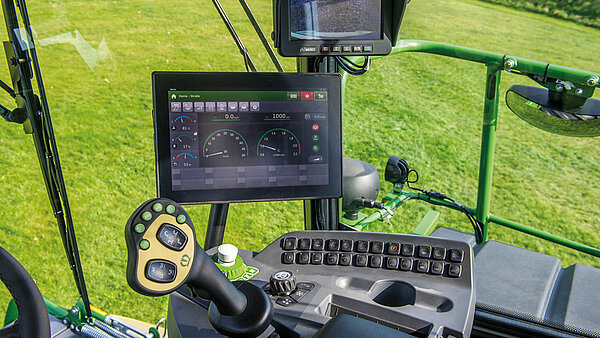
- Extremely spacious and quiet
- Maximum seating and operator comfort
- 360° panoramic view
- Optimum visibility from the raised cab (option)
It takes a comfortable working place to stay fit and alert during those long working days. The spacious Silent Space cab offers such an ideal environment. Providing generous space to the operator and a passenger, it provides a fully air-conditioning and an absolutely functional working place. The exclusive LiftCab offers an unprecedented panoramic view from a height of up to 70 cm.
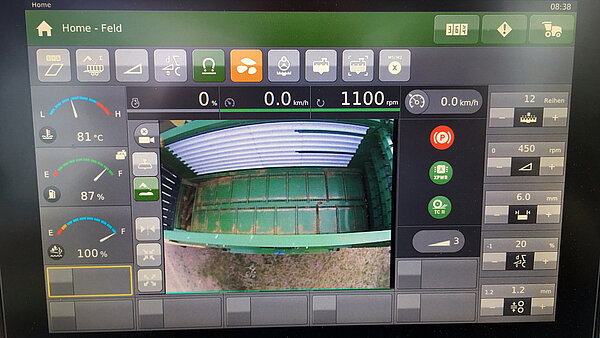
The big 12-inch terminal with USB drive and a video input records all the machine data and displays them on the high-definition colour screen. The screen can show the footage from the reverse drive camera and the camera on the spout.
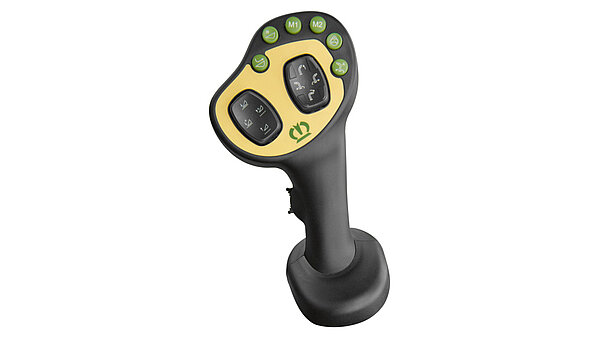
The joystick feels pleasant in driver’s hand. With more than 20 functions programmed to it, the stick not only controls ground speed and direction of travel but also the header and spout.
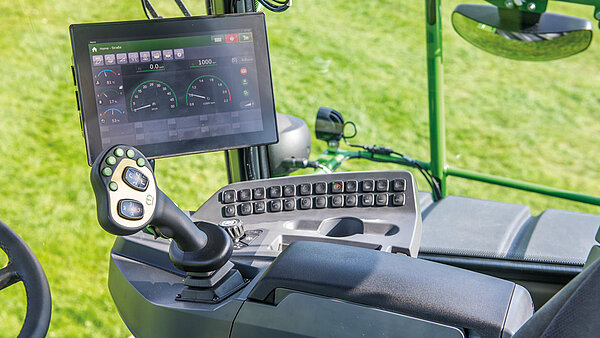
All controls including the joystick, the screens and the terminals are designed to ergonomic standards and in easy reach from the operator seat.
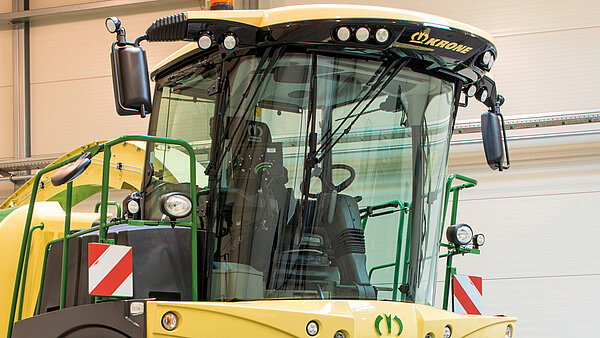
Three optional windscreen wipers on the windscreen, two on the side windows and one on the rear window ensure a clear view in all weather conditions. All wipers are available with water spray nozzles. Perfect illumination is provided by 16 floodlights (H9), while an LED package with 23 working lights is available as an option.
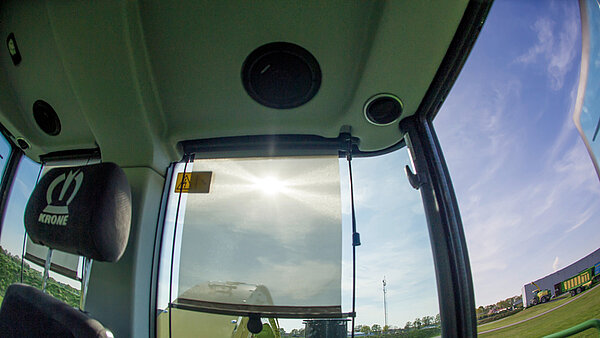
Sun blinds are available for the side and rear windows to protect you from the sun and heat.
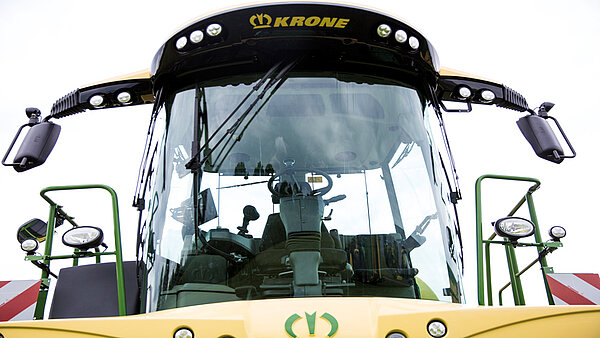
The wide cab with its narrow, rearward-mounted bars offers plenty of space as well as optimum allround visibility, even for headers with large working widths. The double-insulated floor lowers the noise level at the workplace and therefore provides greater comfort.
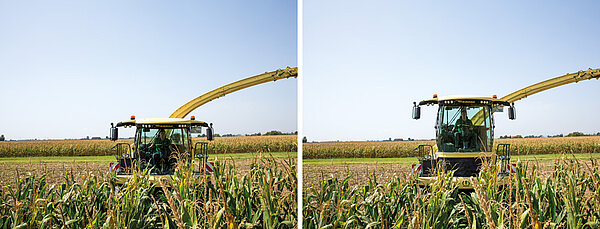
Superb visibility: If the BiG X is specified with a LiftCab, it will be possible to raise the complete cab to any height up 70 cm. From the raised position operators enjoy a full overview of the tall stands and can easily monitor the filling processes. As another advantage, the raised cab increases the distance between the operator and the chopping assemblies thereby reducing the noise level at operator’s ear.
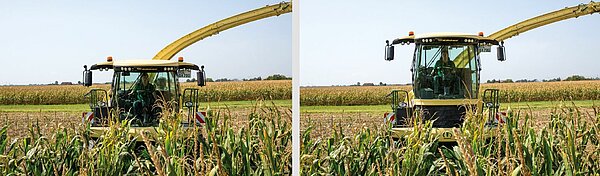
If the BiG X is specified with a LiftCab, it will be possible to raise the complete cab to any height up 70 cm. From the raised position operators enjoy a full overview of the tall stands and can easily monitor the filling processes. As another advantage, the raised cab increases the distance between the operator and the chopping assemblies thereby reducing the noise level at operator’s ear.
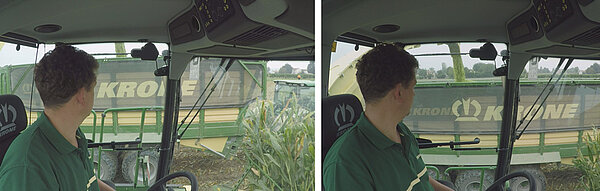
High-sided trailers can be a problem for the forager operator who has to determine when the trailer is filled to capacity. In this situation, raising the cab by 70 cm is a big help. Whether the trailer is travelling alongside or behind the forager, the operator has always a clear view of the load area and can ensure optimum fills.
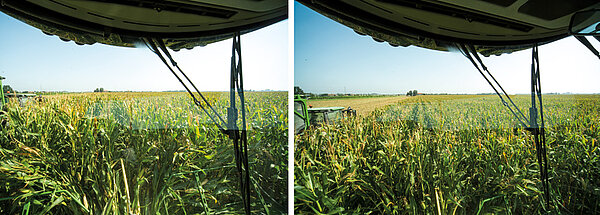
Harvesting high-yielding maize crops, forager operators often are driving up towards an up to 4 m high wall of crop all day. The cab lift allows them to raise their seating position and enjoy a clear view of the field, reducing fatigue and helping them concentrate on the machine and spot any hazardous situations more easily.

The LiftCab is activated from the seat at the touch of a button and is then raised hydraulically to the desired height.
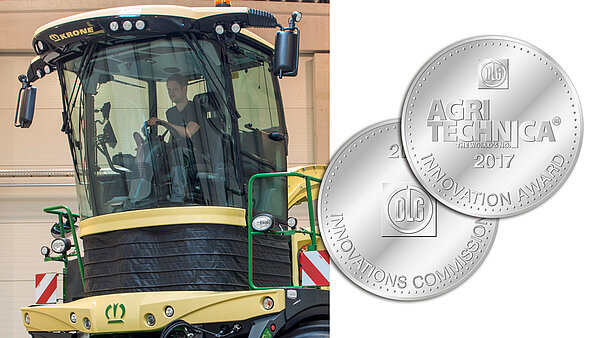
The cab is mounted on a scissor lift which raises and lowers the cabin to any position – infinitely variably and within a few seconds. The area under the cab floor is shielded to prevent of dirt and debris.
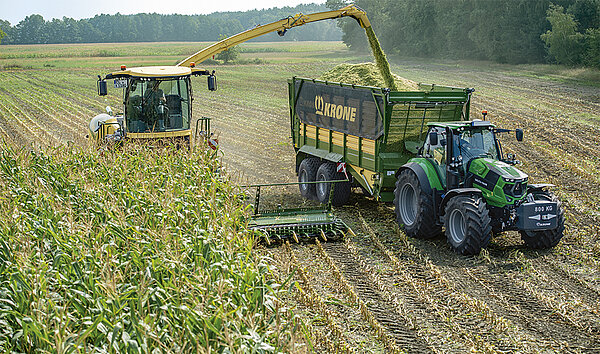
- AutoScan enables operators to adapt the LOC relative to the current maturity of the crop
- ConstantPower ensures optimum fuel economy at maximum throughput
- XtraPower increases engine power on demand
- EasyLoad supports operators in filling the harvest fleet trailers to capacity
- RockProtect protects the forager from damage by stones
- Steer with a joystick and enjoy maximum comfort in field work
KRONE offers a range of different systems which help utilise our BiG X forage harvesters to their full potential and ease the strain on the operator. The electronic assist systems supply relevant data on the crop and provide reliable Information in extremely difficult position.
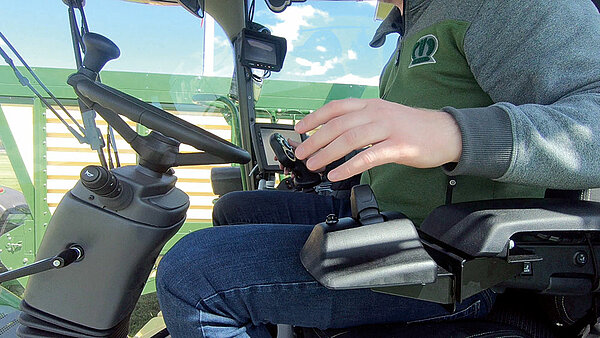
You can also steer the BiG X from a joystick on the left armrest and enjoy a real boost in comfort. Using this joystick takes the hard work out of steering. You are seated in a more ergonomical position and both your arms rest on the armrests for relaxed and fatigue-free work. Thanks to proportional control, the steering is accurate and convenient.

As an option it is possible to adjust the counterblade automatically and from the cab. Based on a knock sensor that measures the gap between the counterblade and the chopping blades and a rotary encoder that triggers two motors that adjust the counterblade, the system reduces operator stress as he or she can concentrate on the work at hand. At the same time, it is also possible to adjust the counterblade manually from the external control unit.
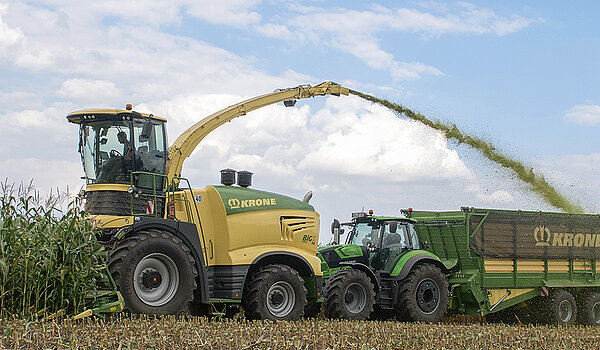
- GPS Guidance for automatic steering
- CropControl for accurate yield metering
- KRONE NIR Control dual measures moisture and nutrients on the move
- AutoCalibrate calibrates the BiG X yield metering system in the field
- KRONE SmartConnect is a standard feature for convenient data management
The ISOBUS steering system guides the machine automatically along the preset way line. More comfort comes from further systems that measure, log and communicate field-specific crop weight data and moisture levels.
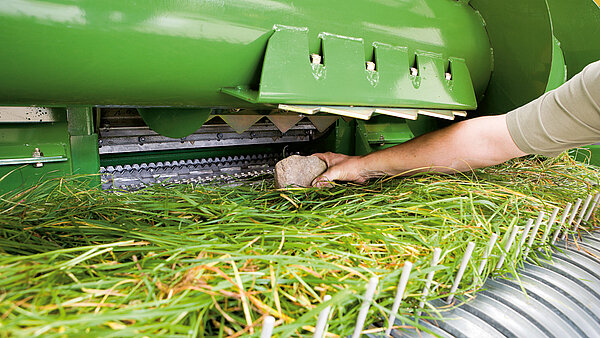
The optional RockProtect system provides intelligent protection from damage by stones as it fully automatically halts the pre-compression rollers within milliseconds after a stone is detected. The sensitivity of the system is set by the operator.
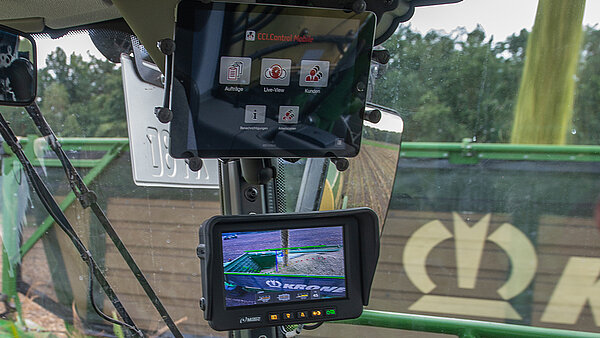
The EasyLoad auto loading system in tandem with the camera-based 3D image analysis make it so much easier to fill low- or high-sided trailers running alongside or behind the harvester. The system controls the open/close spout and the rotate left/right functions and allows operators to select one of several filling strategies. Monitoring all functions from the in-cab screen, operators are more at ease.
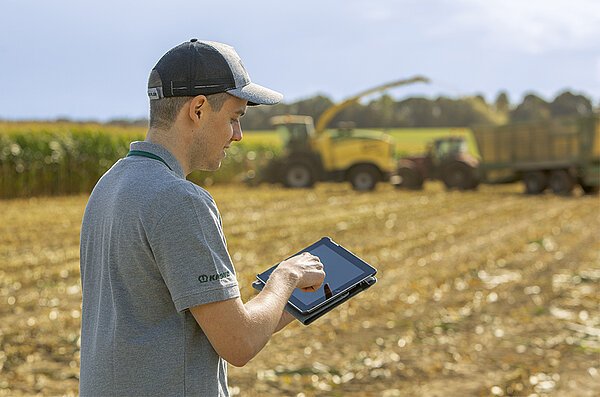
The innovative XtraPower technology allows owners of a BiG X 680 to book more engine power power (50 hp or 100 hp) from the new KRONE E-Solutions shops. Once this extra power is booked, it can be retrieved whenever it is necessary to boost throughputs temporarily. The machine must be in field mode and the chopping drum revolving to enable the feature. The XtraPower function is paused when no extra power is needed.
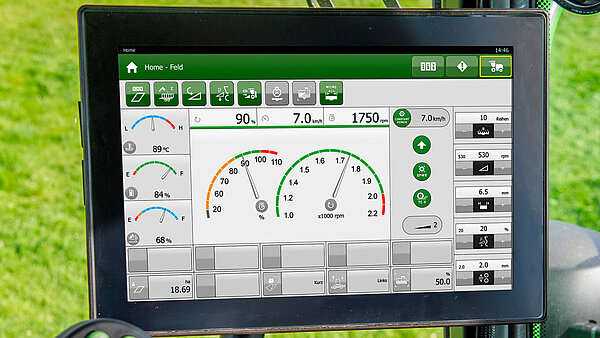
After the operator selects the desired engine load, ConstantPower automatically matches the forward speed to the current stand and yields, easing the strain on the operator and improving fuel economy at maximum throughput. In combination with AutoScan, this system takes the overall quality of chop and machine performance to a whole new level.
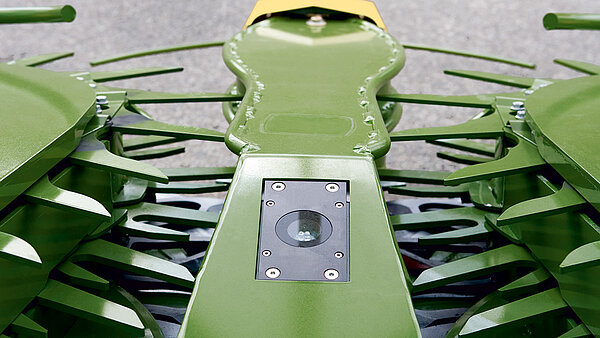
A photo-optical sensor in the middle of the maize header measures the maturity of the plant and automatically adjusts the length of cut. Green maize is cut to longer chops to get more structure and reduce effluent in the clamp. By comparison, dry and brittle maize is cut to short chops to increase compaction. This way, AutoScan eases the load on the operator and reduces fuel consumption by optimizing the length of cut.
Models
BiG X 680 | BiG X 780 | BiG X 880 | BiG X 980 | BiG X 1080 | BiG X 1180 | ||
---|---|---|---|---|---|---|---|
Engine | Liebherr D 9508 | Liebherr D 9508 | Liebherr D 9508 | Liebherr D 9512 | Liebherr D 9512 | Liebherr D 9512 |
configure
|
No. of cylinders | 8 | 8 | 8 | 12 | 12 | 12 |
configure
|
Engine capacity (l) | 16.16 | 16.16 | 16.16 | 24.24 | 24.24 | 24.24 |
configure
|
Continuous engine output (kw/hp) | 505 / 687 | 570 / 775 | 660 / 898 | 720 / 979 | 790 / 1074 | 850 / 1156 |
configure
|
Max. Continuous X-Power chopping output (kW / hp) | 487 / 662 | 550 / 748 | 632 / 860 | 688 / 936 | 758 / 1031 | 818 / 1112 |
configure
|
Max. Continuous Eco-Power chopping output (kW / hp) | 368 / 500 | 368 / 500 | 441 / 600 | 441 / 600 | 441 / 600 | 441 / 600 |
configure
|
configure
|
configure
|
configure
|
configure
|
configure
|
configure
|